Arc-Welding Tips:
Basic Physics applied to Various Processes.
SOLUTIONS with Effective, Powerful Advice
Main Differences among Arc Welding Processes
|
Arc-Welding basic information is presented in this page, to help understanding its main characteristics.
A large group of different methods use the electric arc as a source of heat for welding.
Pressure is not used, generally, but filler metal may be added as necessary.
In a previous page on Welding Processes, a short review was offered of the main processes used for welding.
Here we are going to propose a Beginners Guide with a few Tips, to outline the uses of different kinds of Arc Welding processes and also to enter into some more details.
For a thorough Introduction to Welding visit the NEW Page
on Welding Overview.
Readers seeking more advanced understanding can read our NEW Pages on Process-selection and on Process-optimization.
It should be remembered that under this term (Arc-Welding) a large number of different processes can be described, having in common only the fact that all make use of an electric arc as their localized source of heat.
Why is heat required?
If we describe a joining process like welding as a way to cause a number of different pieces of material to become a unified whole, by producing the intimate union of their atoms, we easily realize that it is not enough to put them close together.
Many hindrances have to be overcome: surface roughness and oxidation, paint, lubrication, impurities and imperfections prevent those atoms to become close enough to realize the (metallurgical) union that is required to keep the parts together and to transmit loads among them.
The use of heat, with or without applied pressure, helps to produce melting and intermixing of the constituent atoms, realizing the intimate contact needed for making stable and strong joints.
Heat however can produce detrimental effects like surface oxidation, or other negative influences on the properties of the base metal, that may ruin the usefulness of the results, and that must be therefore taken into account when planning an Arc Welding process.
Arc-Welding Basics
The arc is part of an electric circuit including the workpiece, the electrode, the conducting cables called leads, and the power supply or source that provides the electric energy with the properties needed for welding, essentially low voltage and high current.
The intense heat, locally produced by the arc, readily melts the base metal forming a weld.
The arc is struck between the workpiece and the tip of the electrode which may be consumable, if its material is intended to melt and become part of the weld pool together with part of the molten base metal, or non consumable, if it is meant only to support the arc and provide heat, not metal.
In this last case, if only base material is melted, and if no other metal is supplied, the weld is called autogenous.
Alternatively, filler metal of suitable kind, form and size may be added manually or mechanically to the hot part of the arc, without being part of the electric circuit, to melt in the weld pool.
What is an electric arc?
The electrodes are the terminals delimiting the arc. In the case of Arc-Welding, one of the electrodes is generally the workpiece, the part being welded, the other being the electrode proper, from which the arc is issuing.
Electric current is a streaming flow of elementary particles which bear a negative charge, called electrons. Atoms include electrons and other elementary particles.
In metals, and particularly in certain types known for their elevated electrical conductivity, some electrons can freely move between different atoms, when an electric field is applied to the circuit.
An arc is essentially the visible discharge of electric current flowing in air, between two electrodes, through a column of ionized gas called a plasma.
Ionized means not neutral, intending that the atoms composing that gas, mainly air plus the atoms of all the elements liberated by the welding process, became charged positively by losing electrons. The positive ions move, in that same plasma column, in opposite direction to that of the electrons.
Polarity
Power Sources supply the needed welding current for Arc-Welding through specific connections intended to make a firm and strong contact with the welding cables. In the simplest set up, one cable connects to the workpiece, the other to the electrode.
If the power source is a simple transformer, it supplies alternating current, (at the frequency of 50 or 60 Hz [Hertz] or times per second), running from zero to a maximum and then back to zero, from where it proceeds to the maximum in the opposite direction, generally represented graphically with a sinusoidal line.
In this case the two connections of the power supply are interchangeable, as they are alternatively positive and negative.
However if the power source supplies direct current for Arc-Welding, there is a difference between the two connections, having an important bearing on how the heat is partitioned between the electrode and the workpiece.
If the cable issuing from the negative connection makes contact with the electrode holder and with the electrode, the connection is called Direct Current Electrode Negative or DCEN, (Straight polarity).
In this case the connection of the power supply is singled out with the minus or negative symbol (-) and the electrode acquires that polarity. The area of the electrode from which electrons are rushing out in the arc, is called the cathode.
The area of the workpiece bombarded by the electrons coming from the cathode is called the anode, and makes contact, in the above set up, with the other connection of the power supply, indicated with the positive symbol (+).
In this case most of the heat of Arc-Welding, valued at about 70%, develops in the workpiece, while only about 30% results concentrated in the electrode.
Conversely changing the polarity to Direct Current Electrode Positive (DCEP) (Reverse Polarity) drives most of heat (~70%) to the electrode side and the rest (~30%) to the workpiece.
One can say that for any given electrode diameter, the maximum current usable (before the electrode itself collapses) is much greater with Electrode Negative (EN) than with Electrode Positive (EP).
However this is only one of the consideration to be taken into account. In welding practice shape and penetration of the weld obtained are more important than the current carrying capacity of any given electrode.
When selecting a suitable electrode for Arc-Welding a certain job, one should know the maximum current compatible with the actual polarity in direct current.
Expressing the same concept in another way, one can say that the cathode loses heat by the emission of electrons. In other words electrons rushing out of the electrode remove heat from it, as if they were cooling it, and that is the reason why higher currents are possible.
The main Arc-Welding processes are now briefly introduced hereafter.
SMAW
Shielded Metal Arc-Welding (SMAW), also called stick welding, is one of the most versatile and used Arc-Welding processes. The equipment is among the simplest and least costly for welding processes.
The application, however, risks to be expensive because the manual operation, requiring a certain measure of skill, is quite slow and needs frequent breaks to change electrode and to remove slag. Reduced duty cycle may also contribute to limited deposition efficiency.
It uses a metal arc, or an arc that transfers material, between a covered electrode and the workpiece. The bare electrode end is clamped in an electrode holder, kept in the welder's skillful hand who strikes and maintains the arc to perform useful welding work.
The consumable electrode, called also the stick, is a straight length of a metal wire, covered, for most of its length with a mixture of various components, applied by extrusion.
The materials of the covering, liberated by the heat of Arc-Welding provide arc stabilizing, shielding, fluxing and deoxidizing functions. Furthermore they generate a liquid protective slag that floats on the molten metal and solidifies to protect the hot weld.
The arc is struck by briefly striking the electrode onto the workpiece and retracting it for a short distance. The heat melts the metal core and burns the covering. A weld pool is readily formed in the workpiece, where the welder adds new material while keeping a constant arc length.
Different types of coverings exist for providing the advantages needed in certain situations. For Arc-Welding best results, electrodes suitable to applications must be selected, and in general manufacturers recommendations should be followed, including the current type, ac or dc and polarity, to be used for specific electrodes.
The preferred power supply for this process is of constant current type (cc) with at least 60% duty cycle at maximum amperage. Constant voltage (cv) are avoided because maintaining a constant arc length would be almost impossible. See also Power Sources.
Dc is preferred for small diameter electrodes and low welding currents as giving a more stable arc. Also striking may be easier. Maintaining a short arc length as recommended is easier with dc. Mechanical properties and toughness are said to be better with DCEP.
Ac is preferred to limit the consequences of arc blow, the influence of magnetic fields on the arc direction. With ac (alternating current) the voltage drop in long cables would be lower than with dc (direct current).
For further information see our page on Shielded Metal Arc-Welding Tips
An Article on Benefits of Low Hydrogen Filler Metal Electrodes was published (4) in Issue 141 of Practical Welding Letter for May 2015.
Click on PWL#141 to see it.
SAW
Submerged Arc-Welding (SAW) is a mature mechanical process designed for relatively long stretches of weld, especially for thick materials (over 6 mm = 1/4"), to be performed in flat position with elevated weld deposition rate.
The arc is maintained between a continuous, coiled bare metal electrode, and the workpiece, under the cover of granulated flux. Filler metal and flux must be selected as a suitable pair, because both contribute to weld quality.
To keep acceptable quality, depending on requirements, penetration and width of heat affected zone (HAZ) may be controlled by limiting heat input, either by reducing amperage or by increasing welding speed.
Upon melting the flux leaves an easily removable slag on the weld. Several modification exist of the basic process, including those employing multiple electrodes to increase even more the deposition rate. Alternating current or direct current with Electrode Positive (EP) or Electrode Negative (EN) can be used.
An Article on New SAW Technology was published (7) in Issue 137 of Practical Welding Letter for January 2015.
Click on PWL#137 to see it.
For further information see our page on Submerged Arc-Welding Tips.
GTAW
Gas Tungsten Arc-Welding (GTAW or Tig) uses a non consumable electrode held in a special torch, while the protective atmosphere is provided by a continuous flow of argon or helium gas.
It is considered the most versatile among the processes as it permits welding of very thin base metals. It is used manually, in all positions, but can also be installed in mechanical, automated or robotic applications.
Filler metal addition is provided, when required, by feeding manually a bare metal into the weld pool. Power source selection depends on the type of current required. Modern power sources provide maximum versatility in supplying the best waveform required for the application.
Older power supplies had a separate high frequency voltage super imposed on the welding circuit to ease arc ignition at every half cycle of alternating current.
Initially improved power supplies offered square wave ac that performed better than conventional sine-wave ac. With further development of electronic controls, new pulsed arc current are now being offered, with an unprecedented level of control of all parameters.
Pulsed arc allows adjustments of pulse current duration, peak pulse current, background current level and time. The pattern selected should suit the application.
The effects of polarity, especially the electrode positive heating, were briefly discussed above. But another effect should be considered: oxide cleaning, most important when welding aluminum and magnesium, occurs only during the electrode positive portion of the ac cycle.
Advanced power controls permit to adjust for each pulse: the polarity, the current amplitude and its duration. With such versatility and proper programming the electrode will never overheat during the EP phase, while oxidation cleaning will be most effective.
Besides manual filler metal feeding, other mechanical methods can be used if necessary, using cold wire (at room temperature) or hot, preheated wire, to improve productivity.
An Article on Back to Basics was published (3) in Issue 142 of Practical Welding Letter for June 2015.
Click on PWL#142 to see it.
An Article on A new Variant of the GTAW process was published (2) in Issue 147 of Practical Welding Letter for November 2015.
Click on PWL#147.
An introduction to our new page on Welding-certification was published (8) in Issue 148 of Practical Welding Letter for December 2015.
Click on PWL#148.
An Article on Welding Austenitic SMO 254 Stainless Steel was published (4) in Issue 155 of Practical Welding Letter for July 2016.
Click on PWL#155.
An Article on Filler Metal for Stainless Steels was published (4) in Issue 156 of Practical Welding Letter for August 2016.
Click on PWL#156.
For further information see our page on Tig Welding Tips.
GMAW
Gas Metal Arc-Welding (GMAW or Mig) uses a continuously fed consumable electrode under protective cover of a suitable gas or mixture. Usually considered a manual process, it can easily be adapted to mechanical or automated applications.
Productivity results much enhanced by the uninterrupted filler metal supply, of which a vast variety of materials and sizes is available. Current density can be increased, for any given filler wire diameter, to allow very fast welding speed.
When applicable, the consumables and the welding parameters should be selected for maximum weld deposition rate, compatible with the quality requested.
Compared with the process introduced above (GTAW), this one (GMAW) is considered easier to learn and apply, and is much more productive because it can deposit a much larger filler metal quantity in any given time.
Power supplies are usually of the constant voltage (CV) type, and most applications are performed with direct current reverse polarity (electrode positive).
Electrode extension is the length of filler wire between the electric contact tip (inside the torch) and the arc. If it is increased, at any current preset value, more current is used to preheat the wire, and less is available across the arc.
The current at the arc is thus a function of the wire feed speed and of electrode extension. A few different metal transfer modes are indicated as typical for GMAW.
The short circuit transfer mode is obtained at low range of current density. It is recognized by a peculiar buzzing sound. Instructors encourage trainees to recognize the buzzing sound, as an aid to adjust the current. This transfer mode is useful for thin materials, to bridge root openings.
At higher current settings, transfer occurs in the form of a spray of small metal drops, suitable for high deposition rate, generally limited to flat or horizontal positions.
Pulsed Arc-Welding control, offered with modern equipment based on inverter technology, permits fine tuned adjustments requiring deeper understanding and considerable testing on the part of procedure specification developers, to achieve higher productivity.
For further information see our page on Mig Welding Tips.
An Article on Improving GMAW Efficiency was published (2) in Issue 137 of Practical Welding Letter for January 2015.
Click on PWL#137 to see it.
When GMAW is combined with Laser Beam Welding, the synergic process is called Hybrid Welding.
A new Mid December 2014 - Bulletin_103 introduces
Updated Resources on Hybrid Laser Arc Welding.
Click on Bulletin 103 to see it.
An Article on Hybrid Induction Arc Welding was published (2) in Issue 138 of Practical Welding Letter for February 2015.
Click on PWL#138 to see it.
An Article on Large Scale Additive Manufacturing was published (2) in Issue 153 of Practical Welding Letter for May 2016.
Click on PWL#153.
An Article on Pulsed GMAW was published (3) in Issue 163 of Practical Welding Letter for March 2017.
Click on PWL#163.
An Article on A Study on argon/hydrogen blend was published (11) in Issue 169 of Practical Welding Letter for September 2017.
Click on PWL#169.
FCAW
Flux Cored Arc-Welding (FCAW) is quite similar to the above process, except for the flux contained in the continuous hollow electrode. Longer electrode extension should be used, as a rule.
The flux develops, upon burning, protective gases and slag similar to those of the SMAW (stick) process. Slag must be removed upon cooling.
FCAW productivity is much higher in comparison to SMAW, while the composition adjustments with ingredients included in the flux may be comparable.
For welding outdoors, this process may be preferred to GMAW, whose gas shielding is considered less reliable in windy conditions. FCAW fumes are more dangerous to welders' health, and their removal by fume extractors is recommended.
Depending on requirements, this shielding may be considered sufficient, or it may be supplemented by additional protection with inert or active gas mixtures.
In all cases where SMAW would call for the use of low hydrogen electrodes, it is imperative to inquire if comparable low hydrogen content can be assured in FCAW electrodes.
For further information see our page on Flux Cored Arc Welding Tips.
PAW
Plasma Arc-Welding (PAW) is produced with a special torch where the arc is created between a tungsten electrode and the workpiece (transferred arc), or between a tungsten electrode and the constricting nozzle, within the torch (non transferred arc).
In both cases the plasma arc is constricted to pass through an orifice that produces a highly collimated arc column. The arc is more stiff and stable than that of GTAW, and therefore less sensitive to distance variation between torch and workpiece.
Shielding is provided from the ionized gas coming out of the torch as well as from an additional supply of neutral shielding gas from a torch concentric tube.
The constricting orifice concentrates the column and the heat, creating a high power density process, reaching a much higher temperature than that of an open arc process. Such a plasma column can be used to weld plates up to 13mm (1/2") tightly fitted square butt joints, by the keyhole technique without filler metal.
The application of keyhole welding technique for thick materials with minimum preparation translates in increased productivity when compared to GTAW.
Such applications require mechanized set up to control weld speed. Normally in continuous operation the torch is connected to direct current electrode negative (EN). Pulsed current modes may use alternating EN and EP for welding aluminum to profit from cathodic etching for oxide removal. A reported application reports EN duration of 20 ms (milliseconds) vs. EP of 3 ms.
For further information see our page on Plasma Welding Tips.
A derivative process called Plasma Gas Metal Arc Welding uses modified GMAW torches including also a tungsten electrode and a constricting orifice. On this process see the article on page 318 of the new Volume 6A of the ASM Handbook.
EGW & ESW
Two additional processes are briefly mentioned here. Only the first, Electrogas Welding (EGW), is properly presented as an Arc-Welding process.
See Electrogas Welding.
The second one, Electroslag Welding (ESW) is only initiated by an arc but, when this is extinguished, it is then continued by providing heat from the resistance to the passage of electric current through the molten slag.
See Electroslag Welding
Both these processes have many details in common and were developed in parallel, for welding vertical joints of thick plates, by supplying a slowly climbing pool of molten metal confined between the plates edges and moving shoes or water cooled copper dams.
The application of both processes are reserved to thick plates, and their advantages and limitations are quite similar. To determine which of the two has economic advantages relative to the other, detailed cost comparisons need be performed in each specific case.
If you did not yet find what you need, why not typing your question in the following Search Box?
* * *
Watch the following Video on Arc-Welding:
http://vimeo.com/couchmode/user8963979/videos/sort:date/30927376
|
Any questions or comments or feedback? Write them down and send them to us by e-mail. Click on the Contact Us button in the NavBar at top left of every page.
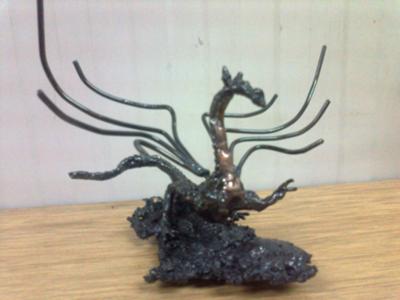
Wig Dragon
[From https://www.welding-advisers.com/my-works.html]
Let us remind you that, if you are interested, we offer a no cost subscription to our Practical Welding Letter and a bonus book in pdf format to be made available for download to your computer on the subject of
PRACTICAL HARDNESS TESTING MADE SIMPLE.
Please Subscribe!.
To reach a Guide to the collection of the most important Articles from Past Issues of Practical Welding Letter, click on Welding Topics.
Back Home
PROCESSES
Site Map
Friction Welding Processes
Friction Stir Welding
Friction Surfacing
Flash Welding Process
Stud Welding
Upset Welding
Resistance Welding Processes
High Frequency Resistance Welding
Projection Welding
Arc Welding Top
Can you think of Business without Boundaries?
Watch the following Video...
Click on the following image to watch the SBI! TV Show!
POWERED BY:
Click on this Logo NOW!
Copyright (©) 2012, 2013, 2014, 2015, 2016, 2017
by Elia E. Levi and www.welding-advisers.com
All Rights Reserved