Brazing-graphite,
challenging development to get success.
SOLUTIONS with Effective, Practical Advice
The Fundamentals Of Brazing Graphite |
Brazing-graphite is performed using complex specialized methods.
Techniques and materials were developed to suit requirements of demanding applications.
There are similarities with Brazing Ceramics, however it is important to stress also the essential differences.
Both graphite and ceramic materials have elevated melting points and relatively low coefficients of thermal expansion (CTE).
However while ceramics are perfectly functional in oxidizing atmospheres, carbon based materials oxidize in the range 450 - 650 °C (842 - 1200 °F) depending on structure and purity.
That is why carbon (graphite) electrodes (as well as Molybdenum metal electrodes) provide useful high temperature heating elements only for vacuum furnaces, while they are rapidly destroyed if heated in air.
Contrary to ceramics, which have little or no porosity open to the surface, carbon often presents large numbers of pores that interfere with Brazing-graphite by sequestering molten brazing alloys away from the joints.
While ceramics are sensitive to thermal shock, graphite is much more resistant because of its higher thermal conductivity, besides low CTE and high strength which increases at high temperatures from 2000 to 2500 °C (3630 to 4530 °F).
At those temperatures graphite and carbon/carbon composites are the only materials that maintain high strength and toughness, provided they are protected from oxidation.
Brazing-graphite Methods
Furnace Brazing graphite is generally considered, although induction brazing can sometimes be applied.
Applications range from nuclear to aerospace, and to many other uses like electronics, fixtures for vacuum furnaces and heating elements, implements for chemical industry, filters for biochemistry, extractive metallurgy and treatment of wastewater.
Several more special applications make good use of unique graphite properties like good electrical conductivity and low friction coefficient (electric motors brushes and switches, bushings and bearings).
But the most advanced applications for aerospace, slowly trickling down to automotive and general industry are for Brazing-graphite of low weight high strength carbon/carbon composites, which consist of carbon or graphite fibers in a carbon or graphite matrix.
These manufactured items show remarkable anisotropy, meaning that their mechanical strength is much lower in the directions that are not fiber reinforced.
Joint design should be based on classic theory for brazed applications (see Brazing Joint Design) but, to provide higher reliability, should be modified with additional, redundant elements like overlap washers, rings, threaded connections etc.
Many of these applications depend on brazing for joining to similar or dissimilar structural elements. One must remember that many of the characteristics that influence Brazing-graphite depend on the technological processes used for obtaining the graphite items in the first place.
Also, for implementations designed to withstand high mechanical stresses at elevated temperatures, brazing applicability depends on the materials used for providing resistance to oxidation.
Due to the low wettability of graphite, it is generally required to pre-coat the graphite elements by various techniques with suitable metallic or intermetallic layers, that contain strong carbide forming elements, displaying more acceptable characteristics.
Wetting or contact angle, expressing the wetting ability of a liquid onto a substrate (where 0 degrees represents complete wettability, and 180 degrees means zero wettability) changes, for any given combination, with brazing temperature and atmosphere: for this reason, for Brazing-graphite, the temperature needs often to be much higher than the melting point of the brazing filler metal.
Furthermore, if the difference in thermal expansion between graphite and the final metal to be brazed is too large, one or more transition pieces must be introduced in the joint to limit the expansion mismatch that risks to crack brazed joints upon thermal cycles.
Several types of filler metals were developed for Brazing-graphite. Typically they contain one or more strong carbide forming elements like titanium, zirconium or chromium.
Although quite a substantial selection of Brazing-graphite filler metals are commercially available, and a lot more were tested that were developed for specific research purposes, any manufacturing project would require a development program where all stages and consumables are tested and appraised for their performance.
The following Table, from selected manufacturers catalogs, displays a few commercial filler metals intended for use at low and moderate application temperatures.
Table
Filler Metals for Brazing Graphite
Name |
Nominal Composition % |
Brazing Range C/(F) |
from WESGO Metals |
Copper-ABA® |
Cu-3Si-2Al-2.25Ti |
1025-1050/(1880-1920) |
Nioro® - ABA™ |
Au-15.5Ni-1.75V-0.75Mo |
970-1020/(1778-1868) |
Ticuni® |
Ti-15Cu-15Ni |
960-1100/(1760-2012) |
Ticuni-60® |
Ti-15Cu-25Ni |
920-980/(1688-1796) |
Silver-ABA® |
Ag-5Cu-1Al-1.25Ti |
920-950/(1688-1740) |
Ticusil® |
Ag-26.7Cu-4.5Ti |
920-960/(1688-1760) |
Cusil-ABA® |
Ag-35.2Cu-1.75Ti |
830-850/(1525-1560) |
Cusin-1-ABA® |
Ag-34.2Cu-1Sn-1.75Ti |
810-860/(1490-1580) |
Incusil®-ABA™ |
Ag-27.2Cu-12.5In-1.25Ti |
720-750/(1328-1380) |
from BrazeTec |
BrazeTec®-CB1 |
Ag-19.5Cu-5In-3Ti |
850-950/(1560-1740) |
BrazeTec®-CB4 |
Ag-26.5Cu-3Ti |
850-950/(1560-1740) |
BrazeTec®-CB10 |
Ag-25.2Cu-10Ti |
850-950/(1560-1740) |
from Titanium Brazing |
TiBraze® 375 |
Ti-37.5Zr-15Cu-10Ni |
850-900/(1562-1652) |
from Lucas Milhaupt |
Hi-Temp 095 |
Cu-9.5Ni-38Mn |
950-1090/(1740-1994) |
Testing is a critical stage in the approval of specific Brazing-graphite solutions. In general published data on obtained mechanical properties refer to very specific processes and can be used only for reference.
To obtain real results one should produce operational prototypes and test them in situations mimicking the actual application. Only then would the design of classic test pieces provide means of process control based on comparison of demonstrated mechanical properties.
New Tables listing a few more Filler Metals for Brazing Graphite and Carbon/Carbon composites at High and Ultra-High temperatures were published (4) in Issue 73 of Practical Welding Letter for September 2009.
Click on PWL#073 for seeing them.
* * *
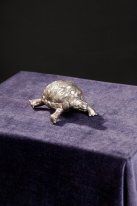
Turtle
[From https://www.welding-advisers.com/images/nature-21438479.jpg]
Any questions or comments or feedback? Write them down and send them to us by e-mail. Click on the Contact Us button in the NavBar at top left of every page.
Let us remind you that, if you are interested, we offer a no cost subscription to our Practical Welding Letter and a bonus book in pdf format to be made available for download to your computer on the subject of
PRACTICAL HARDNESS TESTING MADE SIMPLE. Click on Subscription.
To reach a Guide to the collection of the most important Articles from Past Issues of Practical Welding Letter, click on Welding Topics.
Back Home
Processes
Site Map
Brazing
Brazing Joint Design
Brazing Heating
Brazing Aluminum
Brazing Copper
Brazing Stainless Steel
Brazing Cast Iron
Brazing Titanium
Brazing Ceramic
Brazing Steel
Brazing Nickel
Brazing Magnesium
Brazing Beryllium
Brazing Inspection
If you did not yet find what you need, why not typing your question in the following Search Box?

Brazing-graphite Top
Watch the video...
Click on the following image to watch the SBI! TV Show!
BUILT BY:
Click on this Logo NOW!
Copyright (©) 2009, 2010, 2011, 2012, 2013, 2014, 2015, 2016, 2017
by Elia E. Levi and www.welding-advisers.com
All Rights Reserved