Creep-resistant-steels:
how to select and weld.
SOLUTIONS with Effective, Practical Advice
Creep-resistant-steels for Service under Heat
|
Welding Problem? Solve it! with
Help from a Welding Professional Contact Us.
|
Note: To view Google Ads, Pls.
Right Click and Open in a New Window.
|
Creep-resistant-steels are those providing useful properties even at elevated service temperatures.
Under such conditions, simple carbon steels cannot perform adequately.
According to the American Society of Mechanical Engineers (ASME) Boiler and Pressure Vessel Code, normal carbon steels are suitable for service at temperatures not exceeding 345 °C (650 °F).
At this maximum temperature, per the above Code, the maximum safe design stress shall not exceed 25% of the minimum specified Ultimate Tensile Strength of the steel selected.
ASME Specifications define the types and the properties of several steels, like the following SA 515, SA 516, SA 302, SA 202, and SA 537 for plates, each of them further defined according to Grades or Classes.
It is well known that the mechanical properties of materials depend on temperature.
Specifically the Ultimate Tensile Stress and the elastic limit decrease in various degree with increasing temperature, depending on the type of steel.
The mechanical properties measured at room temperature cannot be used for design purposes for service at elevated temperature.
In fact steels exposed to high temperature may be subject to excessive plastic deformation, for stresses applied for long enough time, even at levels well below the limits acceptable at room temperature.
Note: To view Google Ads, Please
Right Click and Open in a New Window.
|
For use of Creep-resistant steels at elevated temperatures one has to consider:
- the long time stability
- the mechanical properties
- the resistance to oxidation and scaling
- the resistance to corrosive attacks under the service atmosphere.
Furthermore, before finalizing the material selection, one has to take into account fabricability, weldability, maximum run-off temperature, expected life of the construction and cost.
Selection requires particular attention if service is in presence of hydrogen at elevated temperature and pressure.
A short introduction to Heat Resistance was published in Section 2 of Issue 55 of our Practical Welding Letter for March 2008. Click on PWL#055 to see it.
In the same Issue, in Section 7, a short article deals with a related subject, Type IV Cracking.
In practice, to improve the properties of Creep resistant steels, one modifies the metals behavior by alloying them with specified small additions of certain elements.
Chromium, Molybdenum, Vanadium, and other metals have definite influence on favorable modifications of metallurgical microstructure.
For power generation structures, designed to operate for years at elevated temperatures, an accepted criterion was developed.
Different Creep-resistant-steels are evaluated on the base of the results obtained when performing a standard Creep Test.
(Click on the link to see the page).
The test time is established as a period of one hundred thousand hours (corresponding to slightly more than eleven years).
The nominal design stress of any candidate material, when applied continuously on specified specimens at the given temperature, will cause in the said test time period an elongation not exceeding 1% of its basic gauge length.
This is the reference for establishing safe design stresses.
Long Time Creep-resistant-steels
Creep-resistant-steels for high temperature service are those suitable for applications that require exposures between 345 and 815 °C (650 and 1500 °F).
For each one of the approved materials the usual Code establishes the allowable design stress at service temperature.
The following Table lists a few Creep-resistant-steels usually considered for use in the specified temperature ranges.
Table
Creep Resistant Steels
ASME No. |
Composition % | Temperature Range |
Cr |
Mo |
C |
F |
SA 204, grade C |
-- |
0.5 | 430-510 |
800-950 |
SA 302, grade B |
-- |
0.5 | 430-510 |
800-950 |
SA 387, grade 12, class 1 |
1.0 |
0.5 | 455-565 |
850-1050 |
SA 387, grade 12, class 2 |
1.0 |
0.5 | 345-480 |
650-900 |
SA 387, grade 11, class 1 |
1.25 |
0.5 | 455-565 |
850-1050 |
SA 387, grade 11, class 2 |
1.25 |
0.5 | 345-480 |
650-900 |
SA 387, grade 22, class 1 |
2.25 |
1.0 | 455-595 |
850-1100 |
SA 387, grade 22, class 2 |
2.25 |
1.0 | 370-480 |
700-900 |
SA 387, grade 5, class 1, class 2 |
5.0 |
0.5 | 480-620 |
900-1150 |
SA 387, grade 9 |
9.0 |
1.0 | 510-595 |
950-1100 |
SA 387, grade 91 (1) |
9.0 |
1.0 |
540-650 |
1000-1200 |
SA 240 Austenitic (2) |
(2) |
(2) |
595-815 |
1100-1500 |
(1) + Ni, V, Nb, N, Al
(2) - Austenitic Stainless Steels:
Grade 304H 18Cr-8Ni
Grade 316H 16Cr-12Ni-2Mo
Grade 321H 18Cr-10Ni-Ti
Grade 347H 18Cr-10Ni-Nb
Excluding austenitic stainless steels, the other Creep-resistant-steels listed above, in particular those containing Chromium and Molybdenum are all martensitic.
That means they will harden upon quick cooling from the elevated temperatures found in welding.
The usual precaution, to avoid cracking as a consequence of shrinking stresses, is to apply preheating before welding, to decrease the cooling rate from the welding heat.
Then a stress relieving heat treatment is applied as soon as possible after welding, to reduce the residual stresses, especially for thick materials and/or for constrained structures.
Alternatively, a Post Weld Heat Treatment (PWHT) may be specified to improve the properties of the weld and of the Heat Affected Zone (HAZ).
Filler metals are generally similar in composition to the base Creep-resistant-steels, except if post weld heat treatment cannot be performed.
In that case austenitic filler metals (not hardenable) may be preferred to provide more ductility in the weld.
Base metals Creep-resistant-steels may be quite acceptable for elevated temperature service.
It must be noted that welded joints are a potential source of weaker behavior in creep, due to their intrinsic lack of homogeneity and possibly to the presence of weld discontinuities.
The usual practice, as established in codes for nuclear plant components, is to reduce even more the stresses admissible in weldments.
The Mid July 2010 Bulletin 51 was dedicated to online References to articles on Creep Resistant Steels.
It is found, past the regular Issue 83 of Practical Welding Letter. To see it Click on PWL#083 and look for the Bulletin, in the second part of the publication.
A related subject, Risk Based Inspection, concerns the continuing assessment of safe working conditions of plants designed to operate for decades without failures.
It was treated in Section 2 of Issue 57 of Practical Welding Letter for May 2008. Click on PWL#057 to see the article.
The Mid November 2012 of Practical Welding Letter, Bulletin 79 presents online References to Fitness for Service, a related argument.
(Click on the link to see the page).
An Article on How to use Submerged Arc to weld Creep Resistant Steels was published (4) in Issue 142 of Practical Welding Letter for June 2015.
Click on PWL#142 to see it.
Watch the following Video Lecture onCreep Resistant Steels
https://www.youtube.com/watch?v=C9FYcpKoTlk |
* * *
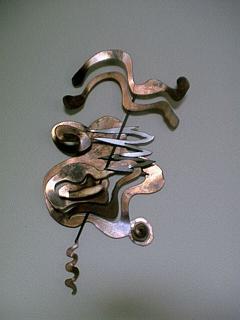
Artwork for Hobby
[From https://www.welding-advisers.com/artwork-for-hobby.html]
Any questions or comments or feedback? Write them down and send them to us by e-mail.
Click on the Contact Us button in the NavBar at top left of every page.
Let us remind you that, if you are interested, we offer a no cost subscription to our Practical Welding Letter and a bonus book in pdf format to be made available for download to your computer on the subject of
PRACTICAL HARDNESS TESTING MADE SIMPLE.
Click on Subscription.
To reach a Guide to the collection of the most important Articles from Past Issues of Practical Welding Letter, click on Welding Topics.
Note: To view Google Ads, Please
Right Click and Open in a New Window.
|
Back Home
Processes
Site Map
Cast Iron Welding
Steel Welding
Alloy Steel Welding
Tool Steel Welding
Stainless Steel Welding
Aluminum Welding
Welding Aluminum, Reprint from HIWT
Magnesium Welding
Titanium Welding
Welding Nitinol
Copper Welding
Heat Resisting Alloys Welding
Joining Lead Tin Zinc
Refractory Metals
If you did not yet find what you need, why not typing your question in the following Search Box?
Creep-resistant-steels Top
Watch the following Video...
Click on the following image to watch the SBI! TV Show!
POWERED BY:
Click on this Logo NOW!
Copyright (©) 2008, 2009, 2010, 2011, 2012, 2013, 2014, 2015, 2016, 2017
by Elia E. Levi and www.welding-advisers.com
All Rights Reserved