Electron-Beam-Welding
High Energy Welding Processes
SOLUTIONS with Effective, Powerful Advice
Electron-Beam-Welding with High Energy Density |
Welding Problem? Solve it! with
Help from a Welding Professional Contact Us.
|
Note: To view Google Ads, Pls.
Right Click and Open in a New Window.
|
Electron-Beam-Welding (EBW) Highlights, and Laser Beam Welding description.
Characteristics. Advantages and Limitations. Similarities and differences.
High power density. Unique repair capabilities. Narrow and deep welds.
Different materials combination allowable.
Favorable costs for special applications.
High quality welds. No contamination. Vacuum sealing. And more...
Information. Comprehensive answers. Reachable further knowledge.
In a previous page on PROCESSES, a short review was offered grouping processes according to some general characteristic. Here we are going into some more detail for HIGH ENERGY DENSITY FUSION WELDING PROCESSES, that are Electron-Beam-Welding (EBW) and Laser Beam Welding (LBW).
Note: To view Google Ads, Please
Right Click and Open in a New Window.
|
The outstanding characteristics of this class of Electron Beam Welding and Laser Beam Welding processes are that their power density stands way out of what is achievable with other more classic methods.
Therefore these processes permit to weld deeper welds with narrower melt volume, and much lower heat input influencing a thinner heat affected zone (HAZ) a quality ensuring quite better properties.
Electron-Beam-Welding explained...
Electron-Beam-Welding (EBW) is the first and foremost high energy density process. It has already a long history of successful applications in a large range of different fields, like aerospace and nuclear but also for general use for most exacting requirements.
Electron-Beam-Welding is generally performed in a vacuum enclosure by striking the joint of two contacting abutting elements with a narrow stream of highly focused energetic and fast electrons which transfer to the metal most of their kinetic energy, thereby elevating the temperature of the target over the melting point of most metals.
Part of the metal is instantly vaporized in Electron-Beam-Welding and a hole (called a "keyhole") is pierced in the metal.
As the keyhole moves with the Electron-Beam along the joint, it leaves in its trail the solidified bead. Another part of the energy goes into producing harmful x-rays as an unavoidable byproduct, which must be taken care of as a safety issue.
The Electron Beam Welding gun is a cylindrical space (kept under high vacuum by powerful vacuum pumps), in the form of the classic triode design, where electrons boil off a heated filament cathode, charged at high negative potential, to be accelerated to high speed by a conforming grid and an anode maintained at ground potential, for safety reasons.
See
ANSI/AWS C7.1/C7.1M:2004
Recommended Practices for Electron Beam Welding
American Welding Society, 11-Dec-2003
130 pages
Which Power Density?...
In Electron-Beam-Welding, the power density of the beam of electrons, concentrated and focused, can reach the value of one hundred millions watts per square centimeter (ten elevated to the eighth power = 108 W/cm2), which is more than that of any other (non explosive!) continuous beam form of energy.
Electrons are negative charged particles, and as such they are influenced and driven around by electromagnetic fields.
This property permits the use of magnetic lenses to converge and focus the beam, so that it will reach the target with the highest power concentrated in the smallest spot, and also permits the use of deflecting coils to manipulate the beam as needed.
The four basic variables controlling the range of energy input into the weld are:
- the Beam current, expressed by the number of electrons striking the workpiece per second
- the Beam accelerating voltage, a measure of the speed of the electrons (in the range of 30 to 70% of speed of light)
- the spot size of the focused Beam, describing the energy concentration at the point of impact
- the welding speed of the relative movement of work vs. Beam.
Tip!: Electron-Beam-Welding is most often performed in vacuum as a consequence of the fact that fast moving electrodes colliding with air or gas molecules could be rapidly dispersed, losing their energy, and become useless.
However there are also Electron-Beam-Welding machines where the electron beam already concentrated and focused, exits the high vacuum space and is permitted to run in air for a very limited distance to the joint.
This is done in automatic systems designed for mass production, with a certain degradation of properties, in order to eliminate the need to evacuate the welding space, operation which would take up too much valuable time.
Straight or curved?...
To perform a weld along a straight or circular line one must provide movement of the Electron-Beam-Welding gun relative to the part. Realizations exist where either the gun moves or the workpiece (on a turntable or on a table moving on two orthogonal axes).
In modern Electron-Beam-Welding equipment provided with Computerized Numerical Control (CNC), relatively limited deflections can be generated by controlling only the deflection coils with no moving parts at all.
Usually, for properly fitted joints, Electron-Beam-Welding is performed autogenously, that is without filler metal addition. If necessary a small amount of extra stock can be supplied by leaving machined protrusions on one of both sides of the joint. Occasionally a thin foil of a different material can be interposed for preventing brittle crack formation.
Tip!: The main advantage of Electron-Beam-Welding is its ability to form deep and narrow joints with limited heat imput, which in turn reduces the extension of the Heat Affected Zone and possible deformations, high stresses or internal cracks.
Other advantages of Electron-Beam-Welding are the vacuum environment, which eliminates possible contamination and reduces porosity, and also permits the sealing of vacuum enclosures, needed for special instruments. The high speed of welding thick joints can be an important economic incentive.
All metals which can be welded by arc processes can be also welded by Electron-Beam-Welding, including exotic ones. Equipment tends to be expensive though, but there are joints which cannot be economically welded by any other process.
Finally Electron-Beam-Welding is successfully applied for repair, overhaul and maintenance of expensive items, because it has almost no influence on nearby material.
On the sides of disadvantages of Electron-Beam-Welding one must include the elevated cost of equipment, the relatively high pump-down time, the need for properly designed joints, special fixtures and expert personnel.
Tip!: There is a flourishing market of refurbished and updated Electron Beam Welders for less demanding applications.
A short note on EBW Repair of a rejected finish machined Casting was published in Section 3 in the June 2004 Issue No. 10 of Practical Welding Letter.
Click on PWL#010 to read it.
Using Filler Metal for Electron Beam Welding is the exception not the rule: but one should know when and how to apply it. An Article on this subject was published in our Practical Welding Letter No. 12, issue of August 2004.
To read the Article click on PWL#012.
A short note on Plasma Window for EBW in air appeared (9.1) in issue 19 of Practical Welding Letter for March 2005. To read it click on PWL#019. Unfortunately it did not yet reach the market.
An Article on Welding in Space was published in the Issue No.24 of Practical Welding Letter for August 2005. To read it click on PWL#024.
An Article on Electron Beam Melting was published in issue 45 of Practical Welding Letter for May 2007. For reading it click on PWL#045.
An Article on High Energy Drilling was published (7) in Issue 49 of Practical Welding Letter for September 2007.
To see the article click on PWL#049.
An Article on Manufacturing Process with EBW was published (7) in Issue 77 of Practical Welding Letter for January 2010.
Click on PWL#077 to read it.
An Article introducing a new page on Additive Manufacturing and online Resources on the same subject was published (8) in Issue 146 of Practical Welding Letter for October 2015.
Click on PWL#146.
An Article on Additive Manufacturing Equals Excitement was published (2) in Issue 159 of Practical Welding Letter for November 2016.
Click on PWL#159.
To receive at no cost all the issues of PWL as they are published, please subscribe.
What about Laser?...
LASER BEAM WELDING (LBW) is another relatively recent development with already quite a remarkable history of successes. A laser (acronym which stands for "Light Amplification through Stimulated Emission of Radiation") is essentially a beam of light, monochromatic (of a single wavelength or color), coherent (all photons are in phase with one another), collimated (concentrated in a narrow beam with low divergence) and, for welding applications, with elevated power density.
The laser is thus a source of thermal energy which can be used for welding when it is of sufficient power density, precisely targeted (focused) on the joint and made to follow the joint path in sequence at proper speed.
Depending on the type of laser and on its power, the thermal energy can be delivered for welding only the surface or through the whole thickness of the joint. With proper adjustments and sufficient power, vaporization temperature of metal is reached, (needed for the keyhole technique) so that the process, besides welding, can be adapted also to hole drilling and cutting.
What is the difference?...
The striking differences as compared with Electron Beam Welding are that laser propagates in air without serious degradation, that it is not influenced by electrostatic or electromagnetic fields, that it can be manipulated with regular optical means like mirrors and lenses (with some exceptions) and that it does not generate harmful x-rays.
Laser generation is a very specialized branch of applied physics which should not be of concern to the welding specialist. For low power, solid state generators are employed, where the production of the beam takes place in the interior of special crystals optimized for this purpose.
For higher power, gas generators much bulkier and complex are used. In both types the fraction of energy of the laser beam output (Electrical to optical power energy conversion efficiency) is quite low when compared to the electrical energy invested for its production.
Laser welding is used in many industries to weld different types of materials and to produce high quality joints. Despite the elevated equipment costs, the economics of the systems have been demonstrated time and again for specialized niches of application.
An Article on Laser Hybrid Welding was published in the December 2004 Issue of Practical Welding Letter #016. To read it click on PWL#016.
An Article on Huge Savings in repairing expensive Scrap Parts explaining how the Laser Beam is used to melt locally metal powders to build or rebuild worn or mismachined parts that would be scrapped otherwise, was published in Issue No. 43 of Practical Welding Letter for March 2007 (section 2). Click on PWL#043 to read it.
An Article on Progress with Laser Hybrid Welding was published in Issue 51 of Practical Welding Letter for November 2007. Click on PWL#051 to read it.
A special Mid Month Bulletin was dedicated to Resources on Laser-Arc Hybrid Welding. Click on PWL#061B to see it.
An Article on Hermetic Seal Laser Welding was published (2) in Issue 77 of Practical Welding Letter.
Click on PWL#077 to read it.
An Article on Additive Manufacturing was published (2) in Issue 106 of Practical Welding Letter for June 2012.
Click on PWL#106 to see it.
A new page on Laser Beam Welding was recently added to our website. Click on the link to see it.
Here are references to some important documents.
ANSI/AWS Z49.1:2012
Safety in Welding, Cutting and Allied Processes (70 pages)
American Welding Society, download from
http://www.aws.org/technical/AWS_Z49.pdf
ANSI/LIA Z136.1-2007
Safe Use of Lasers.
Laser Institute of America / 16-Mar-2007 / 276 pages
ANSI/AWS C5.10/C5.10M:2003
Recommended Practices for Shielding Gases for Welding and Plasma Arc Cutting
American Welding Society, 01-Jan-2003, 72 pages
ANSI/AWS C7.2:1998
Recommended Practices for Laser Beam Welding, Cutting and Drilling
American Welding Society, 01-Nov-1998, 118 pages
NEW RESOURCES
Find some interesting links in a special Mid Month Bulletin Page of our PRACTICAL WELDING LETTER, designed to offer you, our interested readers, the opportunity to search the web quickly and effectively on the subject of Laser Welding. We urge you to explore this rich source of essential knowledge. Online Resources on On Laser Beam Welding and Allied Processes
, presenting Articles, Downloads, Links, References and Information is now available by clicking on PWL#037B. |
Do you need more Online References on additional welding subjects?
Click on Welding Resources.
The Laser Institute...
For a more complete exposure to all aspects of laser production and exploitation including full information on safety requirements, one can visit The Laser Institute site.
Books on Laser Technology can be obtained from the Laser Institute of America (LIA) after browsing their Catalog at
http://www.laserinstitute.org/PDF/pubs/PubsCatalog06Final.pdf
See our new page on Hybrid Welding.
Watch Videos of Electron Beam Welding by performing a Search with the above terms.
If you did not yet find what you need, why not typing your question in the following Search Box?
* * *
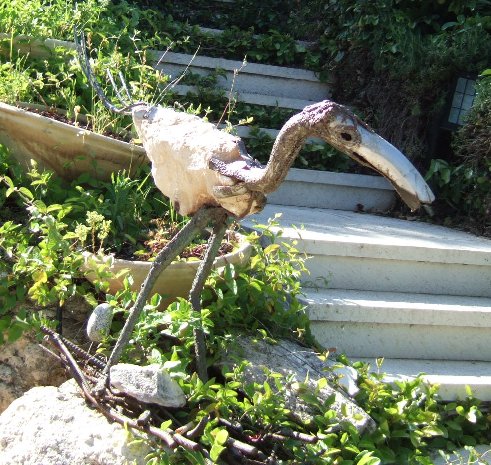
Bird
by Uri Sharon
[From https://www.welding-advisers.com/Hobby-welding.html]
Any questions or comments or feedback? Write them down and send them to us by e-mail.
Click on the Contact Us button in the NavBar at top left of every page.
To reach the Page on EQUIPMENT, click on the underlined item.
To reach a Page, listing the most important Articles from Past Issues of Practical Welding Letter, click on
Welding Topics.
For a FREE subscription to our Practical Welding Letter and for a FREE download, right to your computer of our book in pdf format on
PRACTICAL HARDNESS TESTING MADE SIMPLE, click on Subscription.
As you know hardness may be a critical issue for welding certain materials.
Note: To view Google Ads, Please
Right Click and Open in a New Window.
|
Back Home.
Site Map
PROCESSES.
For any of the other Processes in this Section, by clicking on the underlined item:
Friction Welding Processes
Friction Stir Welding
Friction Surfacing
Flash Welding Process
Stud Welding
Upset Welding
Resistance Welding Processes
High Frequency Resistance Welding
Micro Welding Processes
Additional Processes
Cold welding
Ultrasonic Welding
Explosion Welding
Magnetic Pulse Welding
Forge Welding
Electron-Beam-Welding Top
Watch the following video.
POWERED BY:
Click on this Logo NOW!
Copyright (c) 2003-2008, 2009, 2010, 2011, 2012, 2013, 2014, 2015, 2016, 2017
by Elia E. Levi and
www.welding-advisers.com
All Rights Reserved.
Electron-Beam-Welding and Laser Beam Welding are powerful processes for exacting requirements. Useful for niche applications but also for salvaging expensive items. Have a look...