Micro-welding,
a must for miniature devices.
SOLUTIONS with Effective, Powerful Advice
Anything Visible under Microscope can be Welded
|
Welding Problem? Solve it! with
Help from a Welding Professional Contact Us.
|
Note: To view Google Ads, Pls.
Right Click and Open in a New Window.
|
Can one weld a wire end of 0.05 mm (0.002") diameter?
Sure, by Micro-welding.
But what is Micro Welding?
Micro-welding is a set of different technologies and equipment types that have in common the unique specialty of being able to perform welding on thin or delicate materials.
It is done by depositing welded metal in very small lumps, using minimal heat energy tightly controlled.
The welding processes are designed to maintain tight operational tolerances and not to interfere with product function and quality.
Most of the Micro welding operations are carried out under a microscope with suitable miniature tools to place exactly the hardware elements and filler metal (if present) and to control performance.
Devices where components are welded, need that the equipment used for Micro welding be capable of locating the hardware itself with the required precision.
The due amount of energy for welding is deposited in the exact spot where it is needed, with minimum interference with the surroundings.
Micro-welding for nearly invisible welds...
Note: To view Google Ads, Please
Right Click and Open in a New Window.
|
Although Micro-welding, also called precision welding, is not a standard term identifying a specific process, and recognized as such by the AWS Terms and Definitions Committee, it is a loose description of any process applicable to thin or tiny joints for the purpose of establishing a permanent connection.
Also on the size there is not yet universally accepted consensus. A common definition considers micro welds all those having fusion zone dimensions less than 100 µm (1 micron = 0.001 mm). Another definition would accept welds less than 0.5 mm wide as micro welds.
Practically any welding process suitable to be miniaturized in order to accomplish required diminutive welding could be included in the Micro welding term.
The following processes have been applied with success to Micro-welding:
resistance, flash, arc (tig, mig and plasma) and laser. Also electron beam welding could be considered for miniature welding.
Applications include tiny medical implants, lamps and lighting assemblies, jewelry, dental appliances, aerospace items, hermetic sealing, batteries, thermocouples, wires, TV tube parts, sensing devices, electronic instrumentation, molds and tool build up and many other types of miniature work.
Many experienced welding shops are ready to take in custom specified work of this kind, from those willing to Outsource special production technologies that cannot be done in house.
Other applications, fully automated for mass production, do not require any particular skill on the part of operators.
Resistance Micro-welding
Miniaturized, Micro-welding equipment for spot or seam resistance welding, performs the necessary functions of gripping the elements to be welded between precisely built electrodes that apply pressure and current flow according to schedules designed in advance.
Projection welds are performed using equipment designed to exploit the advantages of using precisely located deformations (bulges) to simplify positioning and alignment of the elements to be joined.
Most of the new equipment has the capability to monitor electrical/mechanical weld parameters but also the internal resistance and to adjust parameters in real time to provide consistent welds.
One can review our page on principles/characteristics of (regular size) Resistance Welding Processes
while descriptions of elements of full size machines can be found on Resistance Welding Equipment.
See also Resistance Welding Tips.
Flash Micro-welding
Applications are reduced versions of well known butt welding equipment for the hot junction of thermocouple wires and for welding together band saw ends. The same elements included in a full size machine are present in equipment of this type made to handle tiny wires.
Machines are available to manufacture decorative chains of precious or regular metals, by welding automatically one by one the formed links.
An overview of the full size version of Flash Welding can be seen on the relevant page.
Arc Micro-welding
Similar to full size types, including GTAW (Tig), GMAW (Mig) and Plasma Arc Welding (PAW), the miniature versions of the same for Micro-welding include power supplies of fractional amperage, generally pulsed, capable of precise control. Mini torches are specially designed and built to permit manual or mechanical handling. These are suitable to perform metal deposition of fine drops or beads in the exact locations required.
As the heat input is minimal, there is no damage to surrounding structures, and the metallurgical influence to Heat Affected Zone is quite limited. Stresses and deformations are almost non existent.
Therefore it is possible to assemble quite easily tiny elements into complex hardware. Or to repair difficult to weld, expensive molds, dies and tools of high alloy steels by the careful placing of build up beads on worn out edges or surfaces.
See the referenced page on the precautions required for regular
Tool Steel Welding.
The selection of the best equipment type for a given job may be quite difficult, although there is a certain overlap among the processes.
GTAW (Tig) Arc Micro-welding uses a nonconsumable tungsten electrode. It is preferred for autogenous (without external filler metal) welds or when filler wire is required only occasionally. Good performance depends on adequate maintenance of the weld arc length. The process is simple and well understood. The small torch can reach recessed locations.
A modification of the GTAW equipment permits orbital or circumferential welds to be performed automatically on small tubes and fittings. The arc runs around from a moving tungsten electrode and welds in one single turn.
See also Tig Welding Tips
GMAW (Mig) Arc Micro-welding electrode is the filler metal itself, which is fed and melted into the arc. It may be used for continuous weld deposition, if a suitable filler wire is available on a spool.
See also Mig Welding Tips.
Plasma Arc Micro-welding uses a nonconsumable electrode that is housed deep into the torch nozzle, and more protected from contamination. It permits to get a stable arc independent of strict control on arc length. It may be useful for welding a very small element on another much more massive. Filler metal, if needed, is provided from the side. Very short duration pulses are available, important for welding fine wires, and tube ends. Gentle arc transfer is suitable for thin and delicate components.
See also Plasma Welding Tips
Dual power supplies are available that support both micro GTAW and micro Plasma Arc Torches. These processes, if a high degree of automation is not required, can be considered less expensive solutions than the following Laser Micro-welding.
On the regular size version one can see the website page on
Arc Welding Processes
and the other page on
Arc Welding Equipment
Laser Micro-welding
The most suitable applications of Laser Micro-welding are those that can be integrated in automatic operations. Small solid state laser sources of limited or fractional power can be employed for micro welding.
The obvious characteristics that provide useful advantages are:
- Heat can be applied from a distance, suitable for deep inside welds
- Laser heat is a form of light that can be transmitted through air (this is an advantage vs. Electron Beam Welding that needs a vacuum chamber)
- No pressure is needed for performing welds
- Energy can be precisely controlled and focused as required
- No contamination is introduced by the process except that a shielding gas may be needed to protect highly reactive materials.
Reflective metals may need a pretreatment in order to be capable of absorbing the major part of the laser energy delivered.
The same laser source can be used for marking letters, numbers and symbols on metal, if directed by suitable hardware and software.
On the regular size version one can see the website page on
High Energy Welding Processes
and the other page on
High Energy Welding Equipment
In conclusion, for every weld requirement of diminutive components one can find a suitable Micro-welding economic process that will provide the correct and reliable technological solution.
Watch the following Video on
Eyeglass repair with microwelding https://www.youtube.com/watch?v=wif96db6xMM |
If you did not yet find what you need, why not typing your question in the following Search Box?
* * *
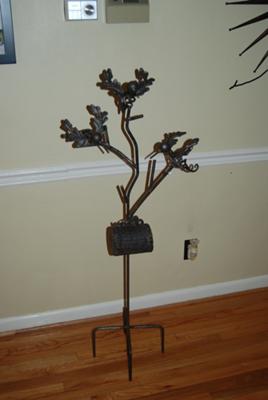
Bird Art
[From https://www.welding-advisers.com/bird-art.html]
Any questions or comments or feedback? Write them down and send them to us by e-mail.
Click on the Contact Us button in the NavBar at top left of every page.
A no cost subscription to our periodic Practical Welding Letter will bring it regularly to you by e-mail, once per month. When you subscribe you will get also a bonus book in pdf format, ready for download to your computer, on
PRACTICAL HARDNESS TESTING MADE SIMPLE.
Click on Subscription.
To reach a Guide to the collection of the
most important Articles from Past Issues of Practical Welding Letter, click on Welding Topics.
Note: To view Google Ads, Please
Right Click and Open in a New Window.
|
Back HOME
Back to Processes
Back to Site Map
to look for an updated Index of Subjects dealt with in this Website.
Additional Processes
Cold welding
Ultrasonic Welding
Explosion Welding
Magnetic Pulse Welding
Forge Welding
Hot Pressure Welding
Roll Welding
Thermite Welding
Tig Welding Tips
Mig Welding Tips
Plasma Welding Tips
Flux Cored Arc Welding Tips
Submerged Arc Welding Tips
Shielded Metal Arc Welding Tips
Oxyacetylene Welding Tips
Micro-welding Top
POWERED BY:
Click on this Logo NOW!
Did you ever ask Can I Succeed Online?
Watch the following Video...
10 000 Miles: The Final Stretch!
Copyright (c) 2005-2012, 2013, 2014, 2015, 2016, 2017 by
Elia E. Levi and www.welding-advisers.com
All Rights Reserved
Micro-welding permits effective metal joining of very thin or delicate elements that cannot stand the heat of regular welding. Precise location of components and short pulses of low energy guarantee good and repeatable results.