Near-net-shape
builds parts point by point.
SOLUTIONS with Effective, Powerful Advice
Electron Beam Direct Manufacturing
|
Welding Problem? Solve it! with
Help from a Welding Professional Contact Us.
|
Note: To view Google Ads, Pls.
Right Click and Open in a New Window.
|
Near-net-shape describes a
group of manufacturing processes.
These are designed to limit the material application.
It is deposited only within an envelope very near to the final volume of the finished item.
This presentation will show methods where the material is applied by fusion welding.
High energy processes like Electron Beam and Laser Beam technology are used successfully.
The advantages to be realized from successful implementations, include:
- reduced part count in complex items,
- economy of weight relative to machining from bulk materials,
- reduction of manufacturing times and costs, and
- improved structural efficiency.
An additional advantage of Near-net-shape processing may derive, where required, by the possibility of using functionally graded alloying, by depositing different materials in specific locations, without changing the manufacturing method.
Near-net-shape to build items drop-by-drop
The idea of depositing material only within the physical boundaries or borders of any given engineering part is not new.
Practical and cost effective methods were realized only in the last few decades.
A small excess material is left in the Near-net-shape, to be removed by final machining, to control dimensions and surface finish to the required quality level.
The development started with the modest goal of repairing expensive items that otherwise had to be scrapped because of worn out material in critical locations.
Typically they were blades of gas turbine engines.
The success obtained with the first applications provided the drive needed to attempt building parts from scratch, with these methods.
Note: To view Google Ads, Please
Right Click and Open in a New Window.
|
Several acronyms were adopted to describe methods related to Near-net-shape processing.
Among them Electron Beam Additive Manufacturing (EBAM), Electron Beam Free Form Fabrication (EBFFF), Electron Beam Direct Manufacturing (EBDM).
The last one, which is not deposited as a trade mark, is considered a general term covering most of the methods that realize the principles described hereafter.
Within the vacuum enclosure traditional for electron beam welders, a wire feeder under full control is set up to supply continuously filler metal directly in the weld pool, at the focal point of the beam.
The part description is displayed in a three dimensional model developed using computer aided design (CAD).
The manufacturing program is derived from the virtual model by another program.
This one instructs the machine to build progressively the part in a succession of locally deposited molten drops, slice by slice.
Thus, in Near-net-shape processing, parts are built by the deposition of new material drop by drop at their exact location.
The commands generate the relative movements of part, wire feeder and focal point across the layer surface, starting from the lowest level, on a suitable support or substrate.
At the same time the welding control program manages the electron beam.
The part is built in the third dimension, by depositing new layers on top of those already done.
Relative movements describe only the geometry of the parts.
To control the physical process one must provide in real time the correct parameters for part speed, wire feed speed, electron beam power and focal position.
The definition of the smallest detail is determined by the filler wire diameter.
Once this is selected, the translation speed, the wire feed speed, the power and the focal position are established and controlled using feedback loops.
The parts can be built using most of aerospace materials including reactive and refractory metals.
The high vacuum environment required for Electron Beam applications, protects most alloys.
Much development work was done on aluminum and titanium alloys.
For building large, massive items, high deposition rates up to 2500 cm3 or
150 in.3 were achieved, while finer details are deposited at lower production rates.
Advanced procedures of thermal simulation permit to evaluate the distribution of residual stresses.
This helps controlling all processing parameters to minimize deformation where objectionable.
A similar Near-net-shape process called Electron Beam Melting, uses metal powders spread upon a surface.
In this case the beam is steered magnetically, and can be split in different beams to cover a given pattern without moving parts.
A new layer of powders is then added and a new beam pattern, at a corrected focus, is run again.
This process is suitable for small parts. Spreading the powder in vacuum may be a problem, as it may tend to be drawn away by the vacuum pumps.
Practical machine realizations where set up to develop and test several critical engineering parts.
The Electron Beam technology was refined with additional applications of state of the art methods.
These include Computer Assisted Design, Process Simulation, and Feedback Control.
Real parts obtained by Near-net-shape processing are then submitted to certification procedures.
To assure they are fit for the demanding applications at the origin of the development effort, the parts must be thoroughly tested.
The achievable advantages have to be ascertained for each new part considered suitable to be built by the process.
It was proved that Near-net-shape processing can indeed deliver the advantages sought for.
The cost of the special processing is justified by the real economies of material and manufacturing costs.
Advance information on this group of processes was presented in an Article on Direct Manufacturing Process with EBW, published at section (7) in Issue 77 of Practical Welding Letter for January 2010.
To see that issue, click on PWL#077.
Readers can find there links to authoritative references.
For a wealth of online Resources on Direct Manufacturing download the
Mid March 2012 Bulletin 71 from PWL#103B.
Note: In the above list of resources one can see that similar applications were developed also using Laser Beam as the source of fusion heat. The applications are probably somewhat overlapping.
An Article on Near-Net Manufacturing was published (11) in Issue 133 of Practical Welding Letter for September 2014.
Click on PWL#133 to see it.
An Article on Direct Write Technology was published (11) in Issue 136 of Practical Welding Letter for December 2014.
Click on PWL#136 to see it.
An Article on Advanced Turbine Airfoil Development was published (2) in Issue 142 of Practical Welding Letter for June 2015.
Click on PWL#142 to see it.
An Article introducing a Website page and a Resource page on Additive Manufacturing was published (8) in Issue 146 of Practical Welding Letter for October 2015.
Click on PWL#146.
An Article on Additive Manufacturing Equals Excitement was published (2) in Issue 159 of Practical Welding Letter for November 2016.
Click on PWL#159.
An Article on Aerospace Applications of Additive Manufacturing was published (2) in Issue 169 of Practical Welding Letter for September 2017.
Click on PWL#169.
* * *
Watch the following Video on
Sciaky's Direct Manufacturing Solution
https://www.youtube.com/watch?v=vfJ-3zGanwE |
* * *
Any questions about Near-net-shape or comments or feedback? Write them down and send them to us by e-mail. Click on the Contact Us button in the NavBar at top left of every page
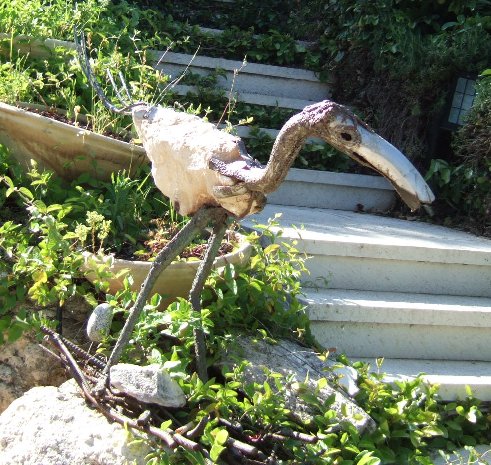
Bird by Uri Sharon
[From https://www.welding-advisers.com/Hobby-welding.html]
If you did not yet find what you need, why not typing your question in the following Search Box?
Let us remind you that, if you are interested, we offer a no cost subscription to our Practical Welding Letter and a bonus book in pdf format to be made available for download to your computer on the subject of
PRACTICAL HARDNESS TESTING MADE SIMPLE.
Click on Subscription.
To reach a Guide to the collection of the most important Articles from Past Issues of Practical Welding Letter, click on Welding Topics.
Note: To view Google Ads, Please
Right Click and Open in a New Window.
|
Back Home
PROCESSES
See the internal links to all pages in the
Site Map
Friction Welding Processes
Friction Stir Welding
Friction Surfacing
Flash Welding Process
Stud Welding
Upset Welding
Resistance Welding Processes
High Frequency Resistance Welding
Projection Welding
Gas Welding Processes
Arc Welding Processes
High Energy Welding Processes
Laser Drilling
Near-net-shape Top
Watch the following video...
How To Build An Online Business
Click on the following image to watch the SBI! TV Show!
BUILT BY:
Click on this Logo NOW!
Copyright (©) 2012, 2013, 2014, 2015, 2016, 2017
by Elia E. Levi and www.welding-advisers.com
All Rights Reserved