Orbital-welding,
Done Almost By Itself.
SOLUTIONS with Effective, Powerful Advice
Orbital Welding for Productive Mechanization |
Welding Problem? Solve it! with
Help from a Welding Professional Contact Us.
|
Note: To view Google Ads, Pls.
Right Click and Open in a New Window.
|
Orbital-welding originated as a special welding technique.
There, the arc from a tungsten electrode is mechanically rotated around a static joint.
Usually for metal tubes to be welded in cramped space.
The need for this development was to substitute manual welding.
Limitations are overcome with an automatic, self regulating process.
It is a process developed to fulfill the need to connect metal tubes (small diameter).
Also for pipes (large diameter), end to end, or to fittings, elbows or other parts as required.
It was developed along the years starting from the basic Gas Tungsten Arc Welding (GTAW).
Later the means were added to move a special torch around the stationary joint to be welded.
Still Later, devices for feeding filler metal were added.
More recently modern power sources are offered with pulsing capability.
Similar processes were developed around Gas Metal Arc Welding (GMAW), Flux Cored Arc Welding (FCAW) and Friction Stir Welding.
The dimensions of weld heads and of mechanical drives moving the torch around the joint are limited, permitting the realization of compact tube assemblies.
Manual welders would have been prevented from reaching with their torch every position needed to accomplish complete welds.
Note: To view Google Ads, Please
Right Click and Open in a New Window.
|
Orbital welding is a mechanized process, magically operating "by itself", apparently without human intervention. Obviously this is not true.
Technically unprepared managers who seek to eliminate real people from production lines, replaced by robots or computers, risk to fall into their own wishful thinking trap.
By witnessing a successful demonstration of Orbital-welding working equipment, they may be deceived into believing that the human expert behind the machine is a needless commodity.
This opinion would perfectly fit their dream of automatic production.
It is true however that an expert operator can supervise a number of less experienced technicians with less demanding qualifications, who are charged with routine work.
But every shop exploiting Orbital-welding should have on its payroll at least one most qualified supervisor to take care of all unexpected problems likely to appear during work.
A more balanced view would assign to modern equipment the advantage of self control capability, relieving the operator from constant attention and intervention.
But it would recognize that proper set up, adjustment and trouble shooting can only be done seriously by someone with adequate instructions, understanding and experience in Orbital-welding.
By recording in the system's memory the successful parameters of a suitable procedure, the same process can be applied repeatedly to produce many welds.
Chances of meeting the requirements of the most strict standards are thus improved, as if performed by qualified welders.
The operator must assure that all the basic physical data (material, dimensions, joint preparation, root gap, cleanliness, set-up) are the same.
Then he has to care for properly connections of the Orbital-welding power source.
The required consumables (shielding gas, filler metal if needed) must be ready for use.
The tungsten electrode has to be correctly ground and mounted in the torch.
The identified prerecorded program must be recalled from memory.
Then the operator has only to push the "start" button to perform his/her duty.
Orbital-welding for increased automatic operation
Before Orbital-welding could be recognized as a reliable production tool, a huge progress had to be done,
The need for the expert welder in charge can be never forgotten.
The outstanding advantages of Orbital-welding reflect the gains:
- in productivity (more welds in less time without welder's fatigue),
- in quality as the movement (position and speed) and the power supply are self-adjusted under automatic (feedback) control,
- in reliability that permits simplified inspection procedures, and possibly
- in the reduction of the number of certified welders to be employed.
Typical applications of Orbital-welding include
- high pressure hydraulic power lines for aerospace systems,
- boiler tube to plate welding,
- heat exchangers,
- processing tubing lines in food and pharmaceutics industries and
- practically any other industry requiring great numbers of repetitive Orbital-welding on tubes or pipes.
In recent times, manufacturers and distributors of Orbital-welding equipment are prepared to give their customers thorough instructions and tutoring.
Shops new to this process may get a lease for a certain time to get accustomed to the technology and to decide if is advantageous to introduce it.
Orbital-welding is by now a mature technology with impressive records of successful applications.
Those who routinely weld tubes and pipes manually, still without enjoying its benefits, are urged to explore how to put it to good use in their industry.
Additional information and links can be found in the following past issues of our Practical Welding letter, in the indicated sections:
PWL#005. (9.2)
PWL#008. (5.3)
PWL#051. (7)
PWL#072. (5.4)(Video)
PWL#091. (5.4)
PWL#095. (5.1)
PWL#100. (5.5)
An Article on Progress in Orbital Welding was published (2) in Issue 107 of Practical Welding Letter for July 2012.
Click on PWL#107 to see it.
An Article on Progress with Laser Orbital Welding was published (2) in Issue 118 of Practical Welding Letter for June 2013.
Click on PWL#118 to see it.
Orbital Welding can be performed also with a Laser Beam Welding process variant called Hybrid Welding.
The new Mid Month Bulletin for December 2014 provides
Updated Resources on Hybrid Laser Arc Welding.
Click on Bulletin 103 to see it.
An Article on Hybrid Induction Arc Welding was published (2)
in Issue 138 of Practical Welding Letter for February 2015.
Click on PWL#138 to see it.
An Article on A new Variant of the GTAW process was published (2) in Issue 147 of Practical Welding Letter for November 2015.
Click on PWL#147.
An Article on Orbital Welding of Tube Heat Exchangers was published (2) in Issue 167 of Practical Welding Letter for July 2017.
Click on PWL#167.
To get every issue of PWL as it is published, please subscribe.
Click on Pipe and Tube Welding for a general presentation of the related subjects.
Watch this Orbital Welding Video
Note: No endorsement or recommendation intended
Orbital Welding by Polysoude - Closed Weld Heads MW https://www.youtube.com/watch?v=joqdlzMCZGA
|
If you did not yet find what you need, why not typing your question in the following Search Box?
* * *
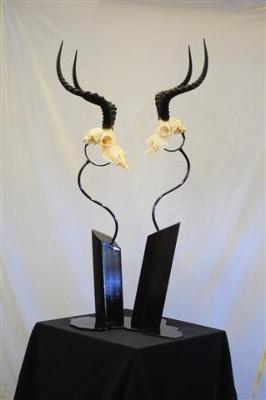
Impala Skulls
[From https://www.welding-advisers.com/dark-continent.html]
Any questions or comments or feedback? Write them down and send them to us by e-mail. Click on the Contact Us button in the NavBar at top left of every page.
Let us remind you that, if you are interested, we offer a no cost subscription to our Practical Welding Letter and a bonus book in pdf format to be made available for download to your computer on the subject of
PRACTICAL HARDNESS TESTING MADE SIMPLE.
Click on Subscription.
To reach a Guide to the collection of the most important Articles from Past Issues of Practical Welding Letter, click on Welding Topics.
Note: To view Google Ads, Please
Right Click and Open in a New Window.
|
Back Home
PROCESSES
Site Map
Friction Welding Processes
Friction Stir Welding
Friction Surfacing
Flash Welding Process
Stud Welding
Upset Welding
Additional Processes
Cold welding
Ultrasonic Welding
Explosion Welding
Magnetic Pulse Welding
Forge Welding
Tig Welding Tips
Mig Welding Tips
Plasma Welding Tips
Orbital-welding Top
Watch the following Video
We Were Just Trying to Make Ends Meet
Click on the following image to watch the SBI! TV Show!
BUILT BY:
Click on this Logo NOW!
Find YOUR Small Business Idea.
Check the following link:
Find It!.
Copyright (©) 2011, 2012, 2013, 2014, 2015, 2016, 2017
by Elia E. Levi and www.welding-advisers.com
All Rights Reserved