Projection-welding:
simultaneous spots exactly located.
SOLUTIONS with Effective, Powerful Advice
Multiple Projections Welded Simultaneously |
Welding Problem? Solve it! with
Help from a Welding Professional Contact Us.
|
Note: To view Google Ads, Pls.
Right Click and Open in a New Window.
|
Projection-welding can be
the
optimal solution,
in certain cases.
The choice of the preferred process depends on availability of
lead time,
materials,
equipment,
workforce,
and by the quantities
to be supplied.
But... how to
select the best process
for a given application?
To answer this question one has first to agree on the meaning of the word "best".
The best welding process is that which satisfies:
- all minimum quality requirements
- at the least cost
- in the due time.
The final selection, however may be determined, even at higher cost if necessary, by constraining circumstances.
If you did not yet find what you need, why not typing your question in the following Search Box?
Note: To view Google Ads, Please
Right Click and Open in a New Window.
|
It helps to know the characteristics of as many processes as practical.
That permits to appreciate the differences among different ways of welding.
And also to evaluate advantages and limitations of available processes.
See the following as an example.
What is this Projection-welding?
Projection-welding is an electrical resistance welding process producing welds by the localized heat generated by the flow of current.
Specially designed projections, embossments or intersections, formed in at least one of the items, determine the points of contact.
The parts to be welded together are pressed by force between simple electrodes, generally flat.
Projection-welding produces solid state bonding or forge welding without fusion, with plastic deformation at the interface.
On embossed sheet metal parts, melting results at the welds, similar to resistance spot welds.
Advantages
Electrode life is generally longer because larger contact areas are used.
One remarks the fact that in Projection-welding the fixtures used are simpler and need less precision than for regular resistance welding.
That is because the points of weld are localized in the parts themselves, and that currents and forces involved are much smaller than for conventional spot welding.
Projection welds are smaller than spot welds. Uniformity of projections permits accurate and consistent location and the final products results more satisfactory.
As projections concentrate heat where needed, this type of resistance welding results suitable to a larger variety of joints than normally considered.
It is possible, with flat electrodes, to weld simultaneously many projections because they concentrate the current where needed.
Closer weld spacing and less overlap is possible, as current is concentrated by projections.
In common with other semi-automatic resistance welding processes the skill required from the workforce is minimal.
Projection-welding is capable of accepting mating elements of widely different thickness.
That is because heating is concentrated at the point of contact, irrespective of members' thickness.
Therefore the possible thickness ratio (typical 6:1 and more) is quite larger than for regular spot welding (3:1 max.).
Raised protrusions of proper dimensions can be formed on metal elements which would have been too thick for regular spot welding.
Occasional surface presence of light rust is less critical, because current breaks through at the protrusions.
Limitations
The limitations point to the need for additional forming operations to prepare the projections.
Furthermore the equipment needs some form of rapid response of the loading system, because the projection collapse brings a loss of force.
To take care of the collapse, the electrodes have to close the gap rapidly to prevent overheating and weld defects.
However production of projections may be more costly than the alternative unless the quantity of parts produced reduces the cost of welding per part.
Close tolerances must be held to obtain acceptable quality, and weld size is limited by projection size
Equipment
Equipment consists in modified resistance welding machines provided with fast follow up head of low inertia capable of exerting a constant force.
Applications
Applications of Projection-welding include sheet metal construction with embossed projections, welding of annular items with machined projections like bushings and nuts onto flat or curved sheets or plates, and cross wire welding.
Materials
Mild and low alloy steel, nickel base alloys, copper and copper alloys are materials suitable for Projection-welding.
Stainless steels and high alloy nickel base materials are difficult to weld by Projection-welding because of the presence of surface oxides that interfere.
Aluminum alloys cannot be joined by Projection-welding because of their tenacious oxides and because these materials soften at low temperature.
Also titanium alloys are excluded because, although their oxides could readily be dissolved, high resistivity and low forging temperature cause early collapse of projections before the weld is established.
Projections
The suggested exact form of projections, the shape of punch and die and the recommended starting schedules can be found in handbooks.
See for example at page 232
ASM Handbook : Welding, Brazing & Soldering
Olson, David L.
9th Ed. Vol. 6
ASM International, 01-Jan-1993
1299 pages
Click to Order.
Alternatives
When the purpose of Projection-welding is to attach an annular body to a surface, other processes could be competitive.
Friction welding may offer definite advantages over Projection-welding, especially regarding the materials weldable, if the production volume is adequate. See Friction Welding Processes.
Otherwise Stud welding, an arc process, may be preferable in certain situations. See Stud Welding.
For orientation, specific Requests for Quotation (RFQ) for each one of the three processes considered (Projection-welding, Friction-welding, Stud-welding) could be issued to specialized manufacturing facilities in view of obtaining and rating accordingly comparable offers for outsourced operations.
An Article on Projection welding of steel nuts was published (3) in Issue 86 of Practical Welding Letter for October 2010.
Click on PWL#086 to read it.
A special Issue of Practical Welding Letter, the Mid June Bulletin No.74, full of Resources on Resistance Welding was published on June 14, 2012.
Click on PWL#106B to see it.
An article on Adaptive Controls for Resistance Seam Welders was published (7) in Issue 139 of Practical Welldib=ng Letter for March 2015.
Click on PWL#139 to see it.
An article on Resistance Projection Welding Revisited was published (3) in Issue 150 of Practical Welding Letter for February 2016.
Click on PWL#150.
An article on Follow-up on VFAW was published (2) in Issue 151 of Practical Welding Letter for March 2016.
Click on PWL#151.
An article on Resistance Welding Nuts to High-Strength Low Alloy (HSLA) Steel was published (4) in Issue 168 of Practical Welding Letter for August 2017.
Click on PWL#168.
To get at no cost each issue of PWL as it is published, please subscribe.
Watch the following Video on
Projection Nut Welding
https://www.youtube.com/watch?v=OgRhvhSJas0 |
* * *
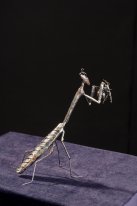
Insect
[From https://www.welding-advisers.com/nature.html]
Any questions or comments or feedback? Write them down and send them to us by e-mail.
Click on the Contact Us button in the NavBar at top left of every page.
Let us remind you that, if you are interested, we offer a no cost subscription to our Practical Welding Letter and a bonus book in pdf format to be made available for download to your computer on the subject of
PRACTICAL HARDNESS TESTING MADE SIMPLE.
Click on Subscription.
To reach a Guide to the collection of the most important Articles from Past Issues of Practical Welding Letter, click on Welding Topics.
Note: To view Google Ads, Please
Right Click and Open in a New Window.
|
Back Home
Processes
Site Map
Friction Welding Process
Flash Welding Process
Resistance Welding Process
Gas Welding Process
Arc Welding Process
High Energy Welding Process
Micro Welding.
Stud Welding.
Resistance Welding Processes
High Frequency Resistance Welding
Gas Welding Processes
Arc Welding Processes
High Energy Welding Processes
Additional Processes
Cold welding
Ultrasonic Welding
Projection-welding Top
Watch the following Video:
SBI!: A New Day
Watch the following Video
POWERED BY:
Click on this Logo NOW!
Follow this Invitation!
Experience C2 power and flexibility in action by clicking SBI! 2.0 For You. Where SBIers share their business-building experiences first-hand. You will realize that there is nothing comparable to SBI! when you read real stories from SBIers who share how C2 has helped them expand, accelerate, build trust and monetize their sites.
|
Copyright (c) 2006, 2007, 2008, 2009, 2010, 2011, 2012, 2013, 2014, 2015, 2016, 2017
by Elia E. Levi and www.welding-advisers.com
All Rights Reserved
Projection-welding may be the most economic solution for certain applications if the conditions are just correct. See all advantages, limitations and alternatives...