Resistance-welding
Processes: know how and when.
SOLUTIONS with Effective, Powerful Advice
Developing Successful Resistance-welding Schedules
|
Welding Problem? Solve it! with
Help from a Welding Professional Contact Us.
|
Note: To view Google Ads, Pls.
Right Click and Open in a New Window.
|
What is in here for me?
Resistance-welding processes are a special class with unique, definite characteristics.
In a previous page on Welding Processes, a short review was offered grouping processes according to some general characteristic, like Pressure or Fusion welding.
Here we are going to enter into some more details for the class of Pressure Welding processes known and described as Resistance Welding processes.
Visit the NEW Page on Welding Overview, for a thorough Introduction to Welding.
Visit also the NEW Page on Process-selection, for Understanding the Selection procedure and
the NEW Page on Process-optimization for improved productivity.
Resistance-welding processes are well established in the manufacturing industry.
A short description of Resistance-welding processes may be useful for refreshing the basics and for building a solid understanding of possible applications.
Resistance-welding is a group of pressure welding electrical processes.
Here the heat necessary to bring locally the metal to the temperature of melting and forging is provided by the passage of an intensive electric current through the parts to be joined.
Note: To view Google Ads, Please
Right Click and Open in a New Window.
|
A presentation of Resistance-welding processes would start with the electrical resistance values that can be measured at the various interfaces present in the secondary circuit of a transformer when two overlapping metallic sheets are held between copper electrodes under a squeezing force.
Other examples of Resistance-welding would include more than two sheets, or less usual setups like that where the edges of roll formed tubes are welded together.
It has long been known that in Resistance-welding, the maximum electrical resistance appears at the interface between the two sheets (while lesser values are present at the other interfaces).
This property is exploited for realizing Resistance-welding processes. The current is the same in the whole circuit.
Heat is proportional to the product of resistance by the square of current and by time. The highest heat is developed where the resistance is at its maximum, exactly where it is needed for this process.
You may want to know which Resistance-welding process is suitable for certain products. Or which are the classic configurations for Resistance-welding. Or what are advantages and limitations.
Or which Specification one could find and where. And which information may be needed on the subject. Whatever you are looking for, we hope you can find here the answer. But if not, drop us a line by e-mail.
Click on the Contact Us button in the NavBar at top left of every page.
If you did not yet find what you need, why not typing your question in the following Search Box?
Advantages and Limitations...
Advantages of Resistance-welding are the fact that it can be performed by unskilled operators, at high speed of production suitable to automatic operation, with proper tools and machines, and that, with automatic controls, high level quality is consistently monitored and obtained.
Filler material is not needed. For certain high strength aluminum alloys, it is practically the only process applicable. (See Aluminum welding).
Limitations are those connected with unbalanced load on the electric grid, especially for single phase Resistance-welding equipment, and the higher equipment cost when compared with other welding processes.
The main parameters...
...influencing the outcome of Resistance-welding are the current intensity in the electrical circuit, the pressure, constant or variable throughout the welding cycle, applied by the electrodes on the surfaces to be welded, and the welding time, usually expressed in cycles of alternating current.
An Article on Spot Weld Lobes was published (2) in Issue 104 of Practical Welding Letter for April 2012.
Click on PWL#104 to see it.
Other important factors to be considered are the surface condition of the metal sheets or elements, the physical and chemical characteristics of the metals, varying widely from type to type, thickness and form of elements to weld, type, form and dimensions of electrodes, the throat length of the machine arms (longer arms reduce current more), and the voltage of the transformer secondary loop.
Taking care of all the factors becomes a major challenge for those whose job is to develop proper schedules capable of producing consistent acceptable results.
In more detail...
SPOT WELDING is a sub-class of Resistance-welding processes where two or three overlapping sheet metal (or wire) elements are joined by individual separate welds generated by the localized heat produced by the resistance to the passage of electric current made to flow across the parts.
In other words, as explained in general for all Resistance-welding, the heat necessary to locally melt the abutting surfaces is obtained from the resistance to flow of a short pulse of high electric current at low voltage, through the parts held together by electrodes developing elevated clamping pressure.
These electrodes do not take part in Resistance-welding: they keep the parts aligned and in place. They apply the pressure required for developing the correct surface resistance at the interface, for containing the molten metal avoiding weld expulsion and for forging the nugget near the end of the cycle.
They convey the electric welding current and, being water cooled, they also dissipate excess heat once the weld is completed, avoiding surface melting.
Immediately after Resistance-welding is completed they may provide a new current pulse for a post weld heat cycle, if necessary, or apply extra forging force, if required.
Electrode composition...
... for Resistance-welding has been established by RWMA.(Resistance Welder Manufacturers' Association). The classification includes copper alloys in Group A, divided in Class 1, 2 and 3, and refractory metals in Group B, divided in classes 10 to 14.
The mechanical and electrical characteristics of each type make each of them best suited to welding a particular material.
Class 1 is used for welding coated carbon steel, aluminum and magnesium.
Class 2 is used for low carbon steel, stainless steel, and silicon bronze.
Class 3 is used for electrodes subjected to high pressures, for heavy sections, for stainless and other heat resistant alloys.
ISO 5182:2008
Resistance welding - Materials for electrodes and ancillary equipment
International Organization for Standardization / 01-Jan-2008 /
Tip!: normally both sides of the structure must be accessible and feedable through the throat depth of the machine, except maybe when specialized electrodes are put in operation as required.
What is this for...
Tip!: For best results the ratio of the two elements thicknesses, if different, should be less than 3 to 1.
The positioning of the spot welds should leave sufficient edge distance to prevent expulsion of molten metal, and between spots the distance should limit the "shunt effect" which detracts a fraction of the current through the already welded adjacent joints, leaving less current to perform the present weld.
Tip!: all Resistance-welding processes of this type need perfectly clean surfaces before welding is attempted, especially for metals like aluminum and stainless steel which tend to develop an oxide layer just by exposure to air.
Therefore one must not leave a long delay after cleaning or interrupt a job in the middle, because the unwelded surfaces tend to deteriorate rapidly even if left in clean air.
There is a certain similarity with the situation of riveted joints, with the rows of ordered spots taking place of the rivets, but here the likeness breaks down.
Whereas rivets are stressed in tension and riveted joints transmit stresses by the force of attrition of one sheet element upon the other, each spot weld opposes only its strength to the force trying to shear it.
Originally the process was developed as less labor intensive than riveting, and also as it was able to provide lighter structures (think of airplane wings).
For welding aluminum, current requirements are higher than for other materials, and controls must be capable of exact timing to ensure consistently high weld quality.
We would like only to stress here that some heat treatable aluminum alloys, which are considered "unweldable" by all other fusion welding processes, because of the negative effect of welding on mechanical properties and resistance to corrosion, are joined exclusively by Resistance-welding when appropriate.
Stainless steels are readily joined by Resistance-welding, except that the particular characteristics of these materials require adaptation of current and time (usually less than what needed for carbon steel) and of pressure (usually higher).
Reason for these differences are the physical and metallurgical properties of these materials.
Tip!: assemblies presenting overlapping sheet metal parts joined by spot welding cannot be successfully plated after welding because of trapping of chemical solutions that later bleed out and cannot be thoroughly washed.
For aluminum alloys the only protective process permitted after Resistance-welding is called Chromic Acid Anodizing.
Preplated (galvanized, nickel-plated or tin-plated) sheet metal may be spot welded, with due attention to the cleanliness of the tips of electrodes.
However, sheet metal covered with insulating plastic layers cannot be joined by Resistance-welding unless the cover is removed, at least locally.
Tip!: if possible a disassembled part (or a mockup) should be provided in advance to the equipment manufacturer, to test the feasibility of the process for the intended use.
And offers from different manufacturers should be compared, possibly by obtaining welded assemblies to test.
The best of it is...
The schedule for a particular job must be developed by knowledgeable people.
But the work is performed by unskilled operators. Sound spots can be produced consistently if surface cleaning is performed per established and proven procedures and if a minimum of quality control testing is performed on test pieces to ensure continuing acceptable results.
Tip!: one should be aware that Resistance-welding machines tend to impose a heavy electrical load on the local grid up to the point of disturbing the operation of other sensitive and precise equipment in the surroundings.
An accepted Specification, which establishes how to develop and certify required Schedules, and gives tables of minimum shear strength requirements is:
ANSI/AWS D17.2-D17.2M-2007
Specification for Resistance Welding for Aerospace Applications
American Welding Society / 04-Jan-2007 / 44 pages
See also:
ANSI/AWS C1.1M/C1.1:2000 (R2012)
Recommended Practices for Resistance Welding
American Welding Society, 01-Jan-2000, 105 pages
and
ANSI/AWS C1.4M/C1.4:2009
Specification for Resistance Welding of Carbon and Low-Alloy Steels
Edition: 2nd
American Welding Society / 22-Aug-2008 / 32 pages
Next comes...
SEAM WELDING which is the Resistance-welding process that provides an uninterrupted series of overlapping spot welds, in a joint which can be made gas tight or liquid tight.
The electrodes are wheels which clamp the sheet metal parts under pressure and transmit pulses of electrical current, while providing also the required rotation or linear advancement of the workpiece.
The wheel materials are the same as those seen before for straight electrodes for spot welding.
Normally seam welding is done on lap joints. Occasionally and with special equipment, also butt seam welding can be performed.
Longitudinal and circular seam welds can be applied to different shapes of workpieces by different machine setups.
Limitations can arise from the buildup of the machine which dictates minimum and maximum diameter for circular welds.
The throat depth of the machine limits the maximum width of one element, if welding from side to side, or the maximum straight length if welding in the perpendicular direction (i.e. for closing a large cylinder).
Machines are quite similar to spot welding counterparts except that means of holding and rotating the circular electrodes are provided.
Better yet...
PROJECTION WELDING is a Resistance-welding process that confines the flow of current on protrusions embossed on one or both of the elements to be joined so that weld location does not depend on exact positioning of workpiece relative to electrodes.
By predetermining number and location of projections one can use simpler electrodes and perform more than one weld in a single welding cycle.
Also the thickness ratio can be made more favorable than for the case where projections are not used, because raised protrusions of proper dimensions can be made on metal elements which would have been too thick for regular spot welding.
Projections can be located more accurately in place and the final products results more satisfactory.
However production of projections may be more costly than the alternative unless the quantity of parts produced reduces the cost of welding per part.
Close tolerance must be held to obtain acceptable quality, and weld size is limited by projection size.
A new page detailing this process is now available.
Click on Projection Welding.
A new page detailing another resistance welding process principles of operation, applications, advantages and limitations is now available.
Click on Upset Welding.
See also:
Resistance Welding Equipment and
Resistance Welding Tips
A special Issue of Practical Welding Letter, the Mid June Bulletin No.74, with Resources on Resistance Welding was published on June 14, 2012.
Click on PWL#106B to see it.
An Article on Capacitor Discharge Welding (2) and another one on Adaptive Controls for Resistance Seam Welders (7) were published in Issue 139 of Practical Welding Letter for March 2015.
Click on PWL#139 to see them.
An Article on Resistance Projection Welding Revisited was published (3) in Issue 150 of Practical Welding Letter for February 2016.
Click on PWL#150.
Follow-up on VFAW was published (2) in Issue 151 of Practical Welding Letter for March 2016.
Click on PWL#151.
An Article on Certified Resistance Welding Technician was published (3) in Issue 154 of Practical Welding Letter for June 2016.
Click on PWL#154.
An Article on Resistance Welding Tips was published (3) in Issue 156 of Practical Welding Letter for August 2016.
Click on PWL#156.
An Article on Update on VFAW was published (7) in Issue 159 of Practical Welding Letter for November 2016.
Click on PWL#159.
An Article on Low Impedance Resistance Welding was published (11) in Issue 162 of Practical Welding Letter for February 2017.
Click on PWL#162.
An Article on Welding of Ultra-Thin Steel was published (2) in Issue 163 of Practical Welding Letter for March 2017.
Click on PWL#163.
An Article on Updating on Resistance Welding was published (2) in Issue 164 of Practical Welding Letter for April 2017.
Click on PWL#164.
An Article on Resistance Welding Nuts to High-Strength Low Alloy (HSLA) Steel was published (4) in Issue 168 of Practical Welding Letter for August 2017.
Click on PWL#168.
To receive at no cost every issue in your inbox as it is published, please subscribe. You will also receive a bonus book on Hardness Testing made simple.
* * *
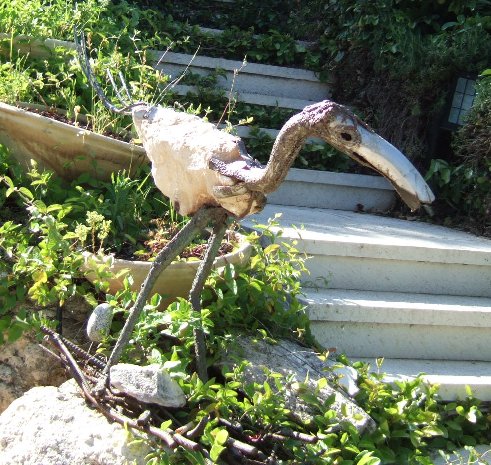
Bird by Uri Sharon
[From https://www.welding-advisers.com/Hobby-welding.html]
Any questions or comments or feedback? Write them down and send them to us by e-mail.
Click on the Contact Us button in the NavBar at top left of every page.
Before closing this page we would like to remind you that we would like to offer you, our interested reader, a FREE subscription to our periodical New Welding Letter.
To reach a Guide, listing the most important Articles from Past Issues of Practical Welding Letter, click on Welding Topics.
And get a FREE book we wrote on PRACTICAL HARDNESS TESTING MADE SIMPLE.
To subscribe and to download the above booklet directly on your computer just click on Subscribe.
This has a lot to do even with welding: as a matter of fact before performing welding on an item it is always advisable to know what the hardness is, to avoid regrettable consequences.
Note: To view Google Ads, Please
Right Click and Open in a New Window.
|
Back Home
Site Map
PROCESSES
Friction Welding Processes
Friction Stir Welding
Flash Welding Process
Stud Welding
Upset Welding
Resistance Welding Processes
Projection Welding
Gas Welding Processes
Arc Welding Processes
High Energy Welding Processes
Laser Drilling
Micro Welding Processes
Additional Processes
Cold welding
Ultrasonic Welding
Explosion Welding
Magnetic Pulse Welding
Resistance-welding Top
Watch the following Video
POWERED BY:
Click on this Logo NOW!
Watch - The Video:
Why Don't I Work From Home?
and also
Think outside the Cube.
Follow this Invitation!
Experience C2 power and flexibility in action by clicking SBI! 2.0 For You. Where SBIers share their business-building experiences first-hand. You will realize that there is nothing comparable to SBI! when you read real stories from SBIers who share how C2 has helped them expand, accelerate, build trust and monetize their sites.
|
Copyright © 2003-2008, 2009, 2010, 2011, 2012, 2013, 2014, 2015, 2016, 2017
by Elia E. Levi and www.welding-advisers.com
All Rights Reserved.
Resistance-welding for unweldable aluminum alloys and for coated steel sheets, to definite shear strength requirements. Have a look...