Thermal-spray
for high performance components.
SOLUTIONS with Effective, Powerful Advice
Protect Surfaces with Thermal Spray |
Welding Problem? Solve it! with
Help from a Welding Professional Contact Us.
|
Note: To view Google Ads, Pls.
Right Click and Open in a New Window.
|
Thermal-spray techniques provide coatings of protective materials to metallic surfaces.
The application of an integral protective cover, endows the surfaces with exceptional resistance.
The usability of unprotected materials is therefore extended by Thermal-spray to useful operation under harsh service conditions.
In this page a comprehensive introduction to the subject is presented.
Advantages and benefits of applying these techniques are explained.
Where appropriate, the implementation of this kind of coatings provides:
- gains in performance,
- extension of useful operational life
- reduction of failure downtime, and
- increases in productivity
by
producing economically improved implements assuring
continuing service life.
These processes have many variants, known also by other names:
- Metal spraying,
- ceramic spraying,
- flame spray,
- metallizing,
- plasma spray,
- plasma coating,
- High Velocity Oxygen Fuel (HVOF) Thermal spray process,
- detonation gun coating
These processes may use spray wire, spray powders, spray electrodes and other consumables.
Thermal-spray is a generic term used for defining a class of processes designed to deposit in a forceful way a layer of finely divided particles sprayed upon a substrate.
The purpose is of building up worn out material or of providing different and enhanced properties on a new surface.
The particles of metals, intermetallics, ceramics or metallic oxides are heated to elevated temperature and projected at high speed by a special gun.
The particles, brought to a hot and semi-molten condition, impinge on the base metal (substrate) and form an adherent coating presenting mechanical interlocking and metallurgical bond, without fusion of the base metal.
Thermal-spray Improve Properties where you need them most
Note: To view Google Ads, Please
Right Click and Open in a New Window.
|
Thermal-spray coatings are used in a wide range of applications:
- For resistance to abrasion, erosion and adhesion wear.
- For thermal barrier coatings to protect other materials and structures.
- For coating easily abradable layers self machined to run-in tolerances.
- For corrosion resistance in air and in marine atmosphere.
- For resistance to high temperature oxidation, erosion and corrosion.
- For providing electric resistance or on the contrary electric conductivity.
- For manufacturing shaped components, one layer at a time.
- For building composite structures of metals and ceramics.
Although Thermal-spray processes involve the use of high temperature and kinetic energy, the effect in heating the workpiece is remarkably limited.
In special cases heating may be completely abolished, by selecting a process variant called Cold Spray.
In general one can obtain a tenacious bond to the deposited layers, without unduly heating the substrate.
In particular thermal sprayed aluminum and zinc have demonstrated successful applications for corrosion protection in industrial atmospheres and in presence of moisture.
The different nature of bonding between Thermal-spray and Hardfacing, consists in the fact that in the latter there is proper fusion of the base metal and dilution of the coating, while in Thermal-spray there is no fusion and limited heating of the substrate.
Special materials for special functions
In certain cases, applications may overlap, in the sense that both Hardfacing and Thermal-spray would present acceptable solutions to the need of providing resistant surfaces.
As usual the availability and economics of implementation would decide for the most appropriate way of realizing the overlay coating.
Tip!: Many different and useful tests were devised for quality control of Thermal-spray processes, generally on specially prepared test pieces.
However one of the best for examination of metallized parts is to submit them to grinding, if required by engineering drawings.
If the coating survives the grinding process without being removed, then the bonding is generally good and adequate for most applications.
Tip!: It should be appreciated that Hardfacing is mostly applied using existing and generic welding equipment.
Thermal-spray in any form requires specialized equipment and consumables, besides special learning and training, so that it may not be readily available.
Outsourcing to subcontracting may be a solution.
Anyhow these processes are unsuited to field application.
Materials can be fed to the heat source either as wire or rod or as powders.
The Thermal-spray equipment though is different in the two cases.
Many different coating materials were developed to cover most different requirements of diverse applications.
The suppliers are ready to provide general information on application and properties of Thermal-spray equipment and products, but would not take responsibility as to the suitability of a certain product for a given application.
The responsibility remains of the developer or of the engineering function, and should be based mainly on previous experience with similar applications and on field tests conducted on prototypes.
Surface preparation.
The surface designated to receive Thermal-spray should be prepared, first by thorough cleaning, and then by roughening by a process that will not contaminate it with oil or other objectionable substances.
One most used preparation process is grit blasting by rough mesh sand or aluminum oxide (or other proprietary products).
Other accepted practices involve rough turning or threading and knurling.
Tip!: One must understand that even traces of oil in the compressed air used for sand blasting, may ruin the whole Thermal-spray process.
Therefore it is imperative to reserve a facility only for preparation to Thermal-spray and to use special oil filters for compressed air.
Check the cleanliness by air spraying on white paper.
One of the most important functions of roughening, besides cleaning and providing new metal surfaces to ensure the best Thermal-spray bond, is to relieve or limit the tensile stresses and the shrinkage that develop in the metallized layer upon cooling on the base metal.
Some materials like molybdenum and un-reacted nickel aluminide are called self-bonding.
They display substantial bond strength even on surfaces not previously roughened, and are used as intermediate layer to promote Thermal-spray bonding of successive layers.
Different processes for ever more exacting requirements
One should remark that in the past the low energy applications of Thermal-spray were also known under the generic name of Metallizing.
In the following, two low power and three high power Thermal-spray processes are presented.
Flame Spray process.
The Thermal-spray wire type gun, normally manually operated but mounted in the tool post of a lathe, consists of a unit which feeds the wire, and of a gas head which controls the flows of fuel gas, oxygen and compressed air.
The wire is fed by knurled rolls, rotated either by an electric motor or by a compressed air turbine.
The gas head provides the flow regulation of the gases through valves, the control of the combustion flame for the wire and of the propellant for the atomized molten droplets.
These are picked up in the gas and compressed air stream and projected with force against the workpiece which typically is not heated much.
It is important to maintain constantly the proper ratio of fuel and oxygen to develop a consistent flame, and to control the wire feed to obtain correct atomization and metal spray.
Arc Spray process.
This Thermal-spray process is carried out with a special torch that feeds two electrode wires, with opposite electrical charges, meeting at their tips where an arc is struck between them, in operation.
The electrode metal is atomized and sprayed by the propelling gas, usually compressed air, unto the substrate.
This process has been used for spraying aluminum or zinc on steel structures to protect them in marine environment.
For best performance the coating is usually sealed with organic compounds.
This Thermal-spray process was a development which had some popularity when it first appeared.
In recent times it has largely been supplanted by more modern and effective processes.
The equipment itself is specialized and cannot be used for other processes, and the properties of the sprayed layers obtained by the following processes are improved.
Plasma spraying.
The first of the Thermal-spray processes characterized by higher energy imposed upon the sprayed particles (in comparison with the previous processes) is Plasma spray.
The hotter flame permits spraying refractory materials that could not be processed at lower energies.
The bond properties of the sprayed layers are higher and the level of porosity and internal defects is lower than with the previous ones, so that there are definite applications for which high energy processes are a must.
As already remarked in previous pages, a Plasma is a very hot gas in a highly ionized form, that is one deprived of some of its electrons by the passage through a powerful electric arc.
A special torch or gun is designed to generate the plasma flame by passing high pressure gas through a constricted or confined arc between water cooled non consumable electrodes, a cathode and a hollow anode nozzle.
The plasma flame meets and carries along the powder particles, fed through the side of the nozzle.
It heats them up to very high temperature, to a molten or plastic state.
It then propels them with high velocity toward the surface to metallize.
The gases used for making the plasma are normally nitrogen with about 10% hydrogen mixed to it.
To provide for proper and continuous Thermal-spray operation, all of the main parameters must be constantly controlled and adjusted.
That is done by automatic provisions once the flame temperature has been selected by changing the ratio of electric current to plasma gas.
With a special arrangement one can spray a buffer layer with one material and then move gradually to a different material.
The proportions of the two change continuously along the thickness of the sprayed overlay: such a development has very useful and interesting applications.
It helps to control and limit stresses due to differences in thermal expansion between the materials.
That improves the adherence of the layers to the substrate.
In modern setups all the functions are computer controlled.
A robot holding the plasma gun points it against the workpiece fastened to a rotating positioner.
The robot is instructed to provide the plasma layers where needed, in the most accurate and repeatable process.
Plasma spray can be applied in air or in a vacuum chamber, and in this case some of the properties are improved.
Detonation gun.
The D-Gun or detonation gun is a piece of Thermal-spray equipment developed to produce superior properties coating, and its name is identified with the process it supports.
It is a water cooled barrel where oxygen, fuel (mostly acetylene) and powder are admitted through valve controlled ports.
The explosive mixture is ignited by a spark at every cycle to propel the heated particles of the powder at supersonic speed.
The substrate to be coated is located at a certain distance from the barrel mouth.
Cycles are repeated with a frequency of a few to at most a few tens a second.
The succession of explosions performing the coating work, produces and elevate level of noise.
Explosions noise must be controlled by locating the equipment in properly insulated facilities.
HVOF.
The High Velocity Oxygen-Fuel (HVOF) Thermal-spray process belongs to those characterized by High Energy.
By accelerating the coating particles to supersonic speed, the process achieves a remarkably high degree of bond strength at the substrate interface, and a very limited level of porosity.
The process is essentially a continuous one: depending on the parts to be coated they may end up hotter then with other processes reviewed here.
Special cooling provisions may be required to prevent overheating.
The equipment is similar to the plasma spray gun with the essential modifications needed to sustain higher temperatures and gas speed.
It was developed in the search for better properties of the deposited layers at a time when the D-Gun was proprietary and enjoyed a monopolistic market position.
The following Documents and Specifications provide important information.
- AWS C2.16/C2.16M:2002
American Welding Society, 01-Jan-2002, 87 pages
Guide for Thermal Spray Operator Qualification
- AWS C2.18-93
American Welding Society, 22-Apr-1993, 43 pages,
Guide for the Protection of Steel with Thermal Sprayed Coatings of Aluminum and Zinc and Their Alloys and Composites
- ASTM B833-09
Standard Specification for Zinc and Zinc Alloy Wire for Thermal Spraying (Metallizing) for the Corrosion Protection of Steel
ASTM International / 01-Oct-2009 / 5 pages
- ASTM B907-09
Standard Specification for Zinc, Tin and Cadmium Base Alloys Used as Solders
[REMOVED reference to Thermal Spraying]
ASTM International / 01-Oct-2009 / 6 pages
- ASTM E1920-03(2008)
ASTM International, 01-Oct-2008, 5 pages
Standard Guide for Metallographic Preparation of Thermal Sprayed Coatings
- ASTM C633-01(2008)
ASTM International, 01-Aug-2008, 7 pages
Standard Test Method for Adhesion or Cohesion Strength of Thermal Spray Coatings
- C2.25/C2.25M:2002
American Welding Society, 23-Apr-2002, 26 pages
Specification for Thermal Spray Feedstock Solid and
Composite Wire and Ceramic Rods
- AWS TSS
Thermal Spraying: Practice, Theory and Application
American Welding Society, 01-May-1985, 194 pages
An Article on Filler Metals for Thermal Spray was published in Practical Welding Letter issue No. 22 for June 2005.
To see the article click on PWL#022.
In the same issue two references are made to a new promising development called Cold Spray that achieves similar or even better results without heating the sprayed particles.
A new website page on this subject was recently added.
Click on Cold Spray to see it.
A short Contribution (Section 11) on Advancements in Thermal Spray was published in the Issue No. 37 of Practical Welding Letter for September 2006.
To see the article click on PWL#037.
An Article on Vacuum Plasma Spray was published in section (2) of Issue 44 of Practical Welding Letter for April 2007.
Click on PWL#044 to read it.
An Article on Cryogenic Nitrogen Cooling for HVOF Spraying was published (2) in Issue 61 of Practical Welding Letter for September 2008.
Click on PWL#061 to read it.
An Article on Low Pressure Cold Spray was published (11) in Issue 67 of Practical Welding Letter for March 2009.
Click on PWL#067 to see it.
An Article on Shock Induced Spraying was published (11) in Issue 68 of Practical Welding Letter for April 2009.
Click on PWL#068 to see it.
An Article on Filler Metals for protecting Steel Structures from Corrosion was published (4) in Issue 71 of Practical Welding Letter for July 2009.
Click on PWL#071 to see it.
An Article on Advances in Thermal Spray was published (11)
in Issue 91 of Practical Welding Letter for March 2011.
Click on PWL#091 to see it.
An Article on Testing of Thermal Sprayed Coatings was published (7) in Issue 93 of Practical Welding Letter for May 2011.
In the same issue, past the regular PWL#093, also the Mid May 2011 Bulletin 61 (PWL#093B) was published, introducing Resources on Thermal Spray.
Click on PWL#093 to see both the Article and the Resource Bulletin 61.
An Article on Plasma Spray Nano Structured Coatings was published (7) in Issue 103 of Practical Welding Letter for March 2012.
Click on PWL#103 to see it.
An Article on Corrosion Protection in the Petrochemical Industry was published (11) in Issue 109 of Practical Welding Letter for September 2012.
Click on PWL#109 to see it.
An Article on Advancements in Spray Coatings was published (11) in Issue 113 of Practical Welding Letter for January 2013.
Click on PWL#113 to see it.
An Article on Filler Metals for Extreme Thermal Spray Coatings was published (4) in Issue 121 of Practical Welding Letter for September 2013.
Click on PWL#121 to see it.
An Article on Plasma Transferred Wire Arc Process was published (3) in Issue 133 of Practical Welding Letter for September 2014.
Click on PWL#133 to see it.
An Article on Direct Write Technology was published (11) in Issue 136 of Practical Welding Letter for December 2014.
Click on PWL#136 to see it.
An Article on Nanocomposite Coatings was published (11) in Issue 142 of Practical Welding Letter for June 2015.
Click on PWL#142 to see it.
An Article introducing a new issue of ASM Thermal Spray Society Newsletter was published (11) in Issue 144 of Practical Welding Letter for August 2015.
Click on PWL#144.
An Article introducing a new issue of ASM Thermal Spray Society Newsletter was published (11) in Issue 148 of Practical Welding Letter for December 2015.
Click on PWL#148.
An Article on Laser Surface Patterning Pre-Treatment was published (11) in Issue 151 of Practical Welding Letter for March 2016.
Click on PWL#151.
An Article on Advances in Thermal Barrier Coatings was published (11) in Issue 153 of Practical Welding Letter for May 2016.
Click on PWL#153.
An Article on Filler Metal for Ni-WC Hardfacing was published (4) in Issue 161 of Practical Welding Letter for January 2017.
Click on PWL#161.
An Article on New issue of iTSSe was published (2) in Issue 165 of Practical Welding Letter for May 2017.
Click on PWL#165.
An Article on The Future of Thermal Spray was published (11) in Issue 167 of Practical Welding Letter for July 2017.
Click on PWL#167.
An Article on Thermal Spray Success Story was published (7) in Issue 168 of Practical Welding Letter for August 2017.
Click on PWL#168.
To subscribe at no cost and receive each month our publication Practical Welding Letter, please click on Subscription.
Watch this Video on
Thermal Spraying with HVOF
https://www.youtube.com/watch?v=ZTTxi3a2OGI |
* * *
Any questions or comments or feedback? Write them down and send them to us by e-mail.
Click on the Contact Us button in the NavBar at top left of every page.
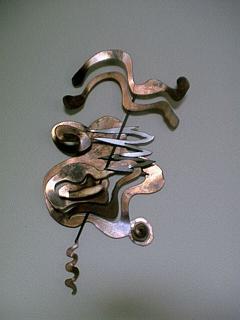
Artwork for Hobby
[From https://www.welding-advisers.com/artwork-for-hobby.html]
Let us remind you that, if you are interested, we offer a Free subscription to our Practical Welding Letter and a Free book (in pdf format) to download to your computer on PRACTICAL HARDNESS TESTING MADE SIMPLE.
Click on Subscription.
It could come in handy, especially for your hard to perform welding or Thermal-spray jobs.
To reach a Guide to the collection of the most important Articles from Past Issues of Practical Welding Letter, click on Welding Topics.
Note: To view Google Ads, Please
Right Click and Open in a New Window.
|
Back Home
Site Map
SAFETY
Hobby and Home Welding
Brazing
Braze Welding
Soldering
Cutting
Hardfacing
Adhesive Bonding
Mechanical Fastening
Shot Peening
Electroslag Welding
Electrogas Welding
Tack Welds
Clinching
Laser Drilling
Stress Relieving
Weld Preheating
Heat Treating
If you did not yet find what you need, why not typing your question in the following Search Box?
Thermal-spray Top
Watch the following video...
Everything You Need To Build
An Online Business! - SBI!
POWERED BY:
Click on this Logo NOW!
Watch - The Video:
Why Don't I Work From Home?
and also
Think outside the Cube.
Follow this Invitation!
Experience C2 power and flexibility in action by clicking SBI! 2.0 For You. Where SBIers share their business-building experiences first-hand. You will realize that there is nothing comparable to SBI! when you read real stories from SBIers who share how C2 has helped them expand, accelerate, build trust and monetize their sites.
|
Copyright (c) 2003-2008, 2009, 2010, 2011, 2012, 2013, 2014, 2015, 2016, 2017
by Elia E. Levi and www.welding-advisers.com
All Rights Reserved.
Thermal-spray processes help improve surface properties, extend useful life, enhance savings, and recondition worn out parts. Essential reading...