Weld-Macro:
Understanding and Learning
SOLUTIONS with Effective, Powerful Advice
Macrographic Examination of Welds |
Welding Problem? Solve it! with
Help from a Welding Professional Contact Us.
|
Note: To view Google Ads, Pls.
Right Click and Open in a New Window.
|
Weld-Macro as explained hereafter is a powerful tool.
It is essential for assessing weld quality and for improving one's welding skills.
Weld-Macro, or Weld Macrographic Examination, is a simplified metallographic technique readily available to anybody.
Visit the NEW Page on Welding Overview, for a thorough Introduction to Welding.
Visit also the NEW Page on Process-selection, for Understanding the Selection procedure and
the NEW Page on Process-optimization for improved productivity.
It can help even the less sophisticated welding shop to observe quality as it is produced, and to maintain or improve it.
Quality is a powerful tool that helps gaining and keeping satisfied customers.
In our page on Welding Testing, two short paragraphs introduce the subject of Metallography, including Weld-Macro.
We explain that if the services available from a metallurgical laboratory are out of reach for the welding shop, an important source of information that could contribute to quality improvement is simply neglected, unfortunately.
Looking inside your welds with Weld-Macro
If you operate a welding shop and do not test your welds, you may be losing insight.
If you think that examining test pieces must be hard and difficult, you should consider again your position.
We propose hereafter a simplified Weld-Macro procedure that should help you overcome your doubts...
If you did not yet find what you need, why not typing your question in the following Search Box?
Why Examine?...
Management (yourself?) may decide that hiring external help for Weld-Macro testing is not a productive expense, and as such it is not really needed.
The expense required to set up and operate a laboratory in house may be considered unjustified: our opinion is that this could be a costly mistake.
It is so because all welding activities that could gain and profit from the assistance and help of a metallographic laboratory, producing examinations of Weld-Macro and Micro sections, would be deprived of a most useful tool.
Such a laboratory should be equipped with all that is needed to examine properly prepared specimens under the optical microscope.
Those running it should be adequately prepared to correctly interpret the different features related to welding, helping the welder to gain insight.
Note - If you make arrangements with a metallurgical laboratory, you may be able to get in a short time your Weld-Macro photographs sent to you by e-mail on the Internet, with comments on the phone...
Note: To view Google Ads, Please
Right Click and Open in a New Window.
|
Even a simple Weld-Macro examination may reveal features readily interpreted to permit improving welding performance.
We recommend to establish in every shop at least the limited capability for Weld Macro examination of welded joint sections.
This could be developed later, if needed, into a fully functioning laboratory.
For welding shop operations mainly concerned with steel, we propose to establish a priority to build a mini-lab., whose capabilities should at minimum permit to examine the following features in Weld-Macro cross sections of test pieces:
- find the weld location
- find the weld borders
- examine the Heat Affected Zone (HAZ)
- measure the weld dimensions
- find and measure obvious internal defects.
An Article on Macro Testing was published in Section 7 in the Issue No. 37 of Practical Welding Letter for September 2006. To see the article click on PWL#037.
To read all Issues of PWL as they are published, please Subscribe and you will also get a bonus e-book on Practical Hardness Testing Made Simple.
To find past Issues of PWL, click on the link to Index of Past Issues of PWL.
What to do with the results?
The information achieved from these Weld-Macro examinations, although partial and incomplete, helps nonetheless in correcting welding procedures.
The purpose is to improve results and obtain satisfactory weld performance.
It is also a demonstration of commitment for quality, a powerful argument in any discussion with customers.
Therefore if assuring quality is a recognized element in the welding shop operation, then one should evaluate the advantages achievable vs. the effort required.
It should be noted that a single Weld-Macro section is not sufficient in general to evaluate welders' performance.
For a test piece length of 150 mm (6"), at least four sections should be performed, preferably in the locations where a visual imperfection is visible externally on the weld bead.
For a tube welded joint, at least four sections are required, at 90 degrees apart. Repeated Weld Macro examinations give also a measure of the consistency of the process performed.
Note - If the welded materials are not steel, but rather aluminum or stainless, then it may be more difficult to prepare the specimens without metallographic equipment.
Etchants (the solutions employed to reveal the micro structures) should be suited to the materials used.
Cross Sectioning
Cutting the weld across (through a transverse plane) for Weld-Macro can be performed by different means.
The simplest would be a hand-saw or a band-saw with running water for cooling. Sawing, if performed carefully with water cooling of the blade, is perfectly acceptable for Weld-Macro.
One has to avoid heating that might alter the surface and introduce unrelated changes (called artifacts).
Therefore flame and plasma cutting should not be considered. Cutting with an abrasive disc is admitted only if thoroughly water cooled.
It is recognized that heavy sections or hard materials are not readily cut by a mechanical saw. If these are the regular work materials to be processed in the shop then one should be prepared to invest in a simple cutting machine built for the purpose.
It has means to clamp firmly thick workpieces, and to section metal items with a water cooled abrasive disc.
Different cutting machines for metallurgical laboratories are available with features suitable for most diverse requirements.
These are defined by the largest dimensions to be cut accepted within the machine and by the power of the motor drive used to operate it.
Generally an enclosure prevents cooling water to be sprinkled outside. Movements, either manual or mechanized, are given to the disc relative to the work to perform the Weld-Macro section. A provision is made for clamping long bars, letting them protrude outside the enclosure.
Mounting
Small Weld-Macro sections must be embedded in a suitable handling device or in plastic media that permit the necessary manipulations as described hereafter.
However sizable chunks of metal can be held by hand without mounting.
Small metallographic specimens that will be examined under a microscope must be prepared in such a way to be put in front of the objective lens. That is easily done if the mounting is of the standard cylindrical shape.
However for the low power enlargement lenses or microscopes that we propose to use for the above purposes with Weld-Macro examinations, any suitable arrangement or clamping device that will hold the specimens in front of the optical instrument may be adequate.
Two types of mountings are used. A simple press, sometimes using a hand operated hydraulic jack, compresses in a cylinder the metallic sample embedded in phenolic or other thermosetting material.
The cylinder is then heated to the temperature that will let the plastic flow. Upon cooling the specimen is extracted, ready to be further processed for Weld-Macro or Micro examination. The entire cycle may last between fifteen and thirty minutes.
The other method involves the preparation of the metallic specimens within simple tubular rubber molds. Then a special formulation epoxy or other two parts mixed plastic material is poured into the molds on the pre-placed metallic specimens and let set, possibly overnight unless a low temperature heating furnace can be used to accelerate curing.
The advantages of the first method are that the specimens are readily available, possibly two or three per hour per mounting press. However an initial outlay for the press is required, and a current expense is required for consumables.
In the second method the initial outlay is minimal, only for purchasing the rubber molds. The consumables are possibly more expensive and less user friendly because of bad smell.
But the number of specimens that can be prepared at one time is limited only by the availability of molds and by the quantity of mixed epoxy that can be prepared at one time.
However the time for setting may last overnight so that the specimens, be they one or many, are not readily available for immediate processing. Once cured though, they can be further prepared all at once.
Many fully equipped metallurgical laboratories have both method available, the selection being made on a case per case basis. But for our welding shop, at least at the start, we consider that mounting is not necessary unless the sections are very small.
Grinding
The raw cut has to be ground and polished. Special equipment is offered to grind the specimens for metallurgical examination.
However, assuming again large sections for Weld-Macro, we could grind the cut surface on any metal grinder (not a hand grinder) capable of giving a flat surface. The only requirement being that the operation be performed while cooling the surface with a suitable liquid.
Clamping the specimens for grinding may be a problem, but a simple vise may do. It is important not to heat up the surface while grinding, as that might introduce unwanted changes in the weld to be examined.
Fine Grinding
A series of grinding means, usually starting with abrasive papers, should then be used to obtain a surface exhibiting the real structure not deformed by excessive local pressure or heat.
Typically simple means are available. They may consist in a manual setup, requiring moving the specimens by hand to and fro.
That is done in a sort of box with four plane supports whereupon self sticking strips are glued, of abrasive paper of increasingly fine abrasive. Dripping water provides the cooling.
Otherwise grinding with abrasive paper is done on mechanized discs. Simple manual devices are available, or more complex instruments for grinding large quantities of specimens.
If if we wish to save on expenses by limiting examination to Weld-Macro only, we will accept whatever finish can be achieved by the simplest means, by manually rubbing the metal specimen on a solid surface covered with progressively finer abrasive papers.
Polishing
For the most exact examination of metallographic specimens at high magnification to detect all the finest features, the best obtainable polished surface should be obtained, and this would entail appropriation of metallurgical polishing machines and proper consumables.
Etching
Serious defects like voids and porosity or cracks may be readily visible on the polished surface of the Weld-Macro without any further treatment.
But for detecting the weld borders we need etching with a proper solution that attacks the metal in such a way that the specific features are made to stand out.
The following reference is available for all information on Macro Etching:
ASTM E340-00e1
- Standard Test Method for Macroetching Metals and Alloys
For our limited purpose as explained above we would propose a single etching solution suitable for common steels and able to reveal what we are looking for.
WARNING: The solution called NITAL, containing from 3 to 5% of Nitric Acid in Methyl Alcohol, should be prepared by a chemist or a pharmacist or by a technician having experience in handling strong acids.
It should be kept in a well marked glass or plastic bottle firmly plugged when not in use, with a label indicating the content and the date of preparation.
WARNING: Keep clear of children. Not to be ingested. Harmful to eyes, mouth, skin.
Use with care by dripping a few drops of the Nital solution on the finely ground Weld-Macro surface to be examined and spread with a wooden spatula, a small brush or a cotton wad wrapped on a stick. Do not touch with your bare hands!
After a few seconds the attack is complete and the outline of the weld should be clearly visible. Rinse the specimen under running water and then dry it.
If the section is not properly etched (under-etched) repeat the procedure for a further short while. If the section is too dark (over-etched), repeat the last polishing and etch again for a shorter time.
Examination
A low power lens or a simple binocular stereoscope should be used with proper lighting. With some trials and exercise it should not be too difficult to learn to perform the whole operation to permit examining the features of the Weld-Macro and to determine if it is acceptable.
Lenses with engraved ruler, raster or grid may be used for determining the important dimension, length of features etc. A Photographic facility may be useful to compare and to document specific items, properly identified.
If different welding procedures are tested one after the other, it is recommended to number the test pieces and to record on a log-book the different conditions employed for welding.
If it is desired to keep the etched specimens for a short while for further reference and comparison, one could use a clear lacquer spray to protect the surface.
Otherwise it will readily rust and the features sought for will not be visible any more (unless the whole polishing and etching procedure is repeated anew).
An Article on Digital Imaging: A Powerful Quality Tool was published (7) in Issue 91 of Practical Welding Letter for March 2011.
Click on PWL#091 to see it.
An Article on Measuring Depth of Decarburization was published (3) in Issue 139 of Practical Welding Letter for March 2015.
Click on PWL#139 to see it.
An Article on Minimizing Alpha Case was published (11) in Issue 152 of Practical Welding Letter for April 2016.
Click on PWL#152.
An Article on Laser Welds in Vacuum was published (2) in Issue 160 of Practical Welding Letter for December 2016. Click on PWL#160.
To read all Issues of PWL as they are published, please Subscribe and you will also get a bonus e-book on Practical Hardness Testing Made Simple.
Conclusion
We recommend to implement the means for examining the quality of welds in cross section.
If the material used is common steel and if the sections are not too thin and not too thick, it should be quite easy to set up a simple facility to see the weld section appearance as Weld-Macro.
The study of the features observed will help improve the quality of the welds performed.
Typical photos can be seen by performing a web Search for Images of Weld macro.
See also:
Metallography of Welds - Application Notes (8 pages)
http://www.struers.com/resources/elements/12/97489/Application%20Notes%20Welding%20English.pdf
* * *
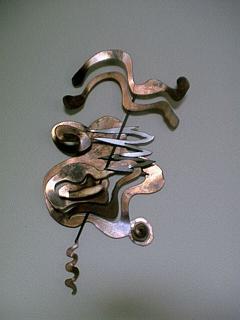
Artwork for Hobby
[From https://www.welding-advisers.com/artwork-for-hobby.html]
Any questions or comments or feedback? Write them down and send them to us by e-mail.
Click on the Contact Us button in the NavBar at top left of every page.
Let us remind you that, if you are interested, we offer a no cost subscription to our monthly Practical Welding Letter and a bonus book in pdf format, downloadable to your computer, on PRACTICAL HARDNESS TESTING MADE SIMPLE.
Click here for your Subscription.
It is always important to know the hardness of any material before welding.
To reach a Guide to the collection of the most important Articles from Past Issues of Practical Welding Letter, click on Welding Topics.
Note: To view Google Ads, Please
Right Click and Open in a New Window.
|
Back Home
QUALITY
Site Map
For anyone of the following Quality subjects, click on the underlined item.
Welding Control
Welding Testing
Welding Inspection
Starting a Welding Shop
Welding Cost Estimate
Welding Distortion
Welding Defects
Welding Failures
Weld Cracking
Welding Liability
Weldability Testing
Visual Weld Inspection
Weld-Macro Top
Watch the Video...
POWERED BY:
Click on this Logo NOW!
Watch - The Video:
Why Don't I Work From Home?
and also
Think outside the Cube.
Follow this Invitation!
Experience C2 power and flexibility in action by clicking Solo Build It! 2.0 For You. Where SBIers share their business-building experiences first-hand. You will realize that there is nothing comparable to Solo Build It! when you read real stories from SBIers who share how C2 has helped them expand, accelerate, build trust and monetize their sites.
|
Copyright (c) 2005, 2006, 2007, 2008, 2009, 2010, 2011, 2012, 2013, 2014, 2015, 2016, 2017
by Elia E. Levi and www.welding-advisers.com
All Rights Reserved.
Weld Macro Examination of test piece sections is an essential element for quality assessment and improvement. It may have important economic consequences. Setting up a simple test facility should be given high priority...