Welding-copper
and copper alloys:
SOLUTIONS with Effective, Powerful Advice
Welding-copper needs Knowledge and Experience.
|
Welding Problem? Solve it! with
Help from a Welding Professional Contact Us.
|
Note: To view Google Ads, Pls.
Right Click and Open in a New Window.
|
Welding-copper is needed for the fabrication of implements made of Copper or Copper Alloys.
These base metals are selected for their outstanding properties like excellent electrical and thermal conductivity, corrosion resistance, ease of fabrication, good strength and fatigue resistance.
Other useful characteristics are being non magnetic, avoidance of sparks (when hit), good bearing properties and pleasant color.
Elevated electrical conductivity, second only to silver, promotes their selection for most of electrical components. High thermal conductivity recommends their choice for heat exchangers.
Various degrees of Copper contain at least 99.3% Cu.
Deoxidized copper includes phosphorus (low P = 0.008%P; high P = 0.02%P).
Except in deoxidized copper and in oxygen free copper (OFC), cuprous oxide in coppers may migrate upon Welding-copper to grain boundaries and affect strength and ductility.
Phosphorus in filler metal combines with oxygen and prevents formation of cuprous oxide.
Depending on the type of copper at hand, autogenous Welding-copper (without filler metal), usable for butt square edge joints up to 3 mm (0.13") might produce lower quality welds because of the oxygen present.
In that case using a phosphorus containing filler metal, capable of scavenging excess oxygen, might be preferable.
Oxyacetylene Welding-copper, despite being technically feasible, is not recommended because its properties are definitely inferior to those obtained by arc welding.
Braze-Welding though might be a suitable alternative.
See Braze Welding.
Note: To view Google Ads, Please
Right Click and Open in a New Window.
|
Beryllium coppers include between 0.6-1.9 %Be, providing high strength or high conductivity.
Beryllium containing coppers develop high strength upon precipitation hardening, which is performed at low temperature (315 or 345 °C, 600 or 650 °F, depending on the type) after welding, without an additional solutioning treatment.
Brasses are copper alloys with zinc (low = 5 %Zn, high = 40 %Zn).
While imparting the required advantages, the alloying additions of zinc reduce weldability, as its low boiling temperature produces toxic vapors that must be removed for safety, and risks to leave porosity in the weld if entrapped.
Bronzes may include up to 10 %Sn and 0.2 %P (Phosphor Bronzes), or up to 10 %Al (Aluminum Bronzes), or up to 3% Si (Silicon Bronzes).
Tin is less volatile and toxic than zinc, but it increases hot-cracking susceptibility in welding. If its oxides become entrapped, the weld strength will be reduced.
Copper Nickel alloys may contain up to 30 %Ni, and nickel-silvers up to 27 %Zn and 18 %Ni.
Special alloys (not suited to welding) may contain addition of lead (Pb), selenium (Se), sulfur (S) or tellurium (Te) for increased machinability.
Beryllium, aluminum and, in less measure, nickel, form adherent oxides that must be removed before and during welding. Beryllium too produces toxic fumes when welded.
Silicon and phosphorus produce deoxidizing and fluxing actions, generally helpful to welding.
All these alloys provide useful properties exploited by Welding-copper in a vast range of applications.
Not all copper alloys display high thermal conductivity (TC). That is given usually as Relative Conductivity in percentage, relative to that arbitrarily established as 100% for alloy C10200 (Oxygen Free Copper - OFC)
at 20 °C.
When Welding-copper, the highest TC alloys require high heat input.
While argon is acceptable as a shielding gas up to 1.6 mm (0.06") thick base metal, for thicker material helium should be preferred because, either pure or mixed (75/25%) with Argon, it contributes to hotter arc.
Preheating may be needed to counter excessive heat loss. Controlled cooling rates help to minimize residual stresses and hot shortness.
Higher thermal conductivity and expansion cause more important distortions, when Welding-copper, than those encountered on similar weldments of carbon steels.
To minimize that, one should use preheat, suitable fixtures, correct sequence and more tack welds than required for steel.
Copper alloys with a wide range between solidus and liquidus may be susceptible to hot cracking because of liquation (or separation) of constituents during solidification.
To minimize that effect one should reduce restraint and welding stresses by applying preheat.
If porosity is an issue in Welding-copper with base metals having low boiling constituents (Zn, Cd, P) one should increase weld speed and use filler metal lacking those elements.
Arc Welding Processes
Shielded Metal Arc Welding (SMAW) with covered electrodes, although feasible for non critical applications, is not recommended for most of the alloys if suitable alternatives are available.
It is acceptable, though, for beryllium copper, aluminum bronze and copper nickel. For Welding-copper, it should be done preferably in flat position.
Covered Electrodes are listed in ANSI/AWS A5.6, see Table III.
Electrodes are used generally with DC electrode positive and use 30-40% more current than for carbon steels of same diameter.
ANSI/AWS A5.6/A5.6M:2008
Specification for Copper and Copper-Alloy Electrodes for Shielded Metal Arc Welding
Edition: 9th
American Welding Society / 06-Nov-2007 / 38 pages
Gas Tungsten Arc Welding (GTAW or Tig) is used with direct current electrode negative (DCEN) for most of the copper alloys.
This arrangement, that concentrates most of heat in the workpiece, permits the use of the smallest electrode diameter for Welding-copper with a given current, contributing to maximum penetration of weld in the base metal.
Electrode material is usually thoriated tungsten (EWTh-2).
Only for Welding-copper of those alloys that develop an oxide layer on the surface (from elements such as beryllium and aluminum), alternating current stabilized by high frequency is preferred.
Backing may be needed, with copper, carbon, graphite or ceramic tape, to prevent loss of fluid weld pool.
GTAW is used for Welding-copper up to 3 mm (0.125") with square butt edge preparation without filler metal, if the base material does not contain low temperature boiling elements (Zn, Cd) or too much oxygen.
For thicker material, bevel edges are machined and filler metal is used.
See Table I.
Watch in the following Video a simple demonstration on: Welding-copper.
Plasma Arc Welding (PAW) has definite advantages vs. GTAW especially for thicker Welding-copper as it permits application of keyhole mode.
(See Plasma Welding Tips).
The electrode is more protected from contamination and the constricted arc provides hotter plasma that reduces HAZ thickness. Filler metals available for GTAW are used also for PAW.
ANSI/AWS A5.7/A5.7M-2007
Specification for Copper and Copper-Alloy Bare Welding Rods and Electrodes
American Welding Society / 12-Apr-2007 / 32 pages
Gas Metal Arc Welding (GMAW) is used for Welding-copper when larger quantities of Filler metal are required. This means thicker joints, although GTAW is preferred for higher quality and thinner Heat Affected Zone.
Direct current electrode positive (DCEP), except for base metals containing oxide forming layers, that interfere with welding as remarked above.
However GMAW, because of not localized, greater heat input, results in increased porosity and lower HAZ strength, particularly in Welding-copper electrolytic tough pitch (ETP) and oxygen free copper (OFC), that don't include residual phosphorus as deoxidizer.
This should be included in the filler metal to improve the weld quality.
Flat position is preferred whenever possible, out of position is reserved for less fluid alloys as aluminum bronzes, silicon bronzes and copper-nickel alloys.
Pulsed spray metal transfer, if available, has proved advantageous for Welding-copper in difficult positions.
This short review of arc welding processes would not be complete without mentioning Submerged Arc Welding (SAW) but it seems still under development, especially for cladding or hardfacing of copper-nickel alloys.
Alternative processes like Friction Stir Welding (FSW) may be preferable and more economic.
Table I
Filler Metal for GTAW
per Spec. AWS A5.7
Filler Metal |
AWS Class |
Base Metal |
Copper |
ERCu |
Copper |
Phosphor bronze |
ERCuSn-A |
Phosphor Bronze |
Aluminum Bronze |
ERCuAl-A2 |
Aluminum Bronze |
Aluminum Bronze |
ERCuAl-A3 |
Aluminum Bronze |
Silicon Bronze |
ERCuSi-A |
Silicon Bronze |
Copper-nickel |
ERCuNi |
Copper-nickel |
Table II
Filler Metal for GMAW
per Spec. AWS A5.7
AWS Class |
Common Name |
Base Metal |
ERCuSi-A |
Silicon Bronze |
Silicon Bronze, Brasses |
ERCuSn-A |
Phosphor Bronze |
Phosphor Bronzes, Brasses |
ERCuNi |
Copper-nickel |
Copper-nickel alloys |
ERCuAl-A2 |
Aluminum Bronze |
Aluminum Bronzes, Brasses, Silicon Bronzes, Manganese bronzes |
ERCuAl-A3 |
Aluminum Bronze |
Aluminum Bronzes |
ERCuNiAl |
... |
Ni-Aluminum Bronzes |
ERCuMnNiAl |
... |
Mn-Ni-Al Bronzes |
RBCuZn-A (a) |
Naval Brass |
Brasses, Copper |
RCuZn-B (a), RCuZn-C (a) |
Low Fuming Brass |
Brasses, Manganese Bronzes |
(a) - Used for Braze-Welding with Oxyacetylene flame, NOT for arc welding
Table III
Filler Metal for SMAW
per Spec. AWS A5.6
AWS Class |
Common Name |
Base Metal |
ECu |
Copper |
Coppers |
ECuSi |
Silicon Bronze |
Silicon Bronzes, Brasses |
ECuSn-A, ECuSn-C (a) |
Phosphor Bronze |
Phosphor Bronzes, Brasses |
ECuNi |
Copper-nickel |
Copper-nickel alloys |
ECuAl-A2, ECuAl-B |
Aluminum Bronze |
Aluminum Bronzes, Brasses, Silicon Bronzes, Manganese Bronzes |
ECuNiAl |
... |
Ni-Aluminum Bronzes |
ECuMnNiAl |
... |
Manganese Ni-Al Bronzes |
(a) - Used for repair welding of castings. ECuSn-C provides greater hardness and strength than ECuSn-A
Welding-copper alloys
Beryllium Copper
Thin sections, up to 13 mm (0.5") of High Strength Beryllium Copper (alloys C17000 and C17200) are welded using GTAW. Mixed Helium Argon is used as shielding gas.
As already mentioned, the cleaning action is obtained by using alternating current, and in this case the electrode is zirconiated tungsten (EWZr) or pure tungsten (EWP) and the tip is balled by melting.
If continuous cleaning is not necessary, that is if the base metal does not contain oxide forming elements, then DCEN (electrode negative) is used with thoriated tungsten electrode (EWTh-2) tapered cone tip that gives a longer tip life and is easier to start the arc.
Note that when this electrode is used with alternating current it causes the arc to wander.
Filler metal of the same composition as base metal is used for Welding-copper.
Preheating up to 200 °C [400 °F] is recommended. Aging heat treatment after welding is applied at 315 or 345 °C [600 or 650 °F)] as required by the specific base metal.
High Conductivity Beryllium Copper (alloy C17500) is more difficult to weld due to its higher melting temperature and less fluidity.
GMAW is used for thickness greater than 6 mm (0.25") but even for less, if more practical. DCEP (electrode positive) is used.
Filler of same composition is preferred but other electrodes can be used if strength is not an issue.
Brasses
Brasses are copper zinc alloys: those with low zinc content are easier to weld than those with higher content. Other elements, like aluminum or nickel, if present, may impair weldability.
GTAW is suitable for thin joints. The filler metal is selected for ease of welding and color matching, if important.
For low zinc, ERCuSn-A is preferred. For high zinc, ERCuSi-A (silicon decreases Zn fumes) and ERCuAl-A2. Zinc is absent in filler metals.
Please remark that the last three filler metals in Table II are intended for Braze-welding with oxyacetylene flame and NOT for arc Welding-copper.
Electrodes for GMAW are the same as for GTAW, except that, because of higher zinc fumes evolution, fume removal provisions must be more effective.
Preheating is seldom necessary, because of the reduced thermal conductivity of these alloys.
SMAW with proper electrodes can be done. If the results obtained are acceptable, matching of compositions is not essential.
Phosphor bronze electrodes have been used for welding low zinc brasses. Low preheating 200-260 °C [400-500 °F] is applied. Narrow and shallow stringer beads are preferred.
Aluminum bronze filler metal is used for high zinc base metal with preheat somewhat higher than above, 260-370 °C [500-700 °F]. To minimize fuming, the arc is directed on the pool and slowly advanced.
Phosphor Bronzes
Phosphor bronzes include up to 10 %Sn (tin). They show good resistance to flowing seawater and to certain acids.
GTAW is used to repair castings but these alloys solidify with large dendritic grains, susceptible to cracking.
To improve results, welds should be peened while still hot, thus reducing shrinkage stresses and cracking.
Argon as shielding gas is adequate and is thought to reduce HAZ size.
Filler metal ERCuSn-A is used or ERCuSi-A for stronger welds.
Preheating is not needed generally, but when it is, a low range of temperatures is enough, 175-200 °C [350-400 °F], with hot peening as advised above.
GMAW is used for thicker Welding-copper joints, with filler ERCuSn-A electrode wire.
Preheating and interpass heating can prevent porosity but it may also increase susceptibility of large grains and risks of hot cracking.
Therefore small weld pool, narrow stringer beads deposited at high travel speed and hot peening are recommended.
SMAW uses covered electrodes ECuSn-A and ECuSN-C with DCEP (electrode positive).
Low preheating 150-200 °C [300-400 °F] and interpass temperature are needed because phosphor bronze are sluggish. Hot peening as suggested above should be applied.
The weldments should then be post weld heat treated for maximum ductility at 480 °C [900 °F] and cooled rapidly.
Aluminum Bronzes
Welding-copper aluminum bronzes is employed for joining and for hardfacing, taking into account their complex composition that includes many different elements.
For multipass welding, GTAW is used with argon and alternating current, stabilized with high frequency, to prevent formation of surface oxides.
For single pass welding DCEN can be used with argon, helium or a mix of the two, for better penetration or faster weld speed.
A specially formulated flux applied on the weld edges can help avoiding oxidation.
Filler metals are used as indicated in Table I above for aluminum bronzes.
Preheating is not needed for sections thinner than 6 mm (0.25"). For thicker joints preheating and interpass heating is done at 150 °C [300 °F].
GMAW is preferred for aluminum bronze when suitable, in all positions.
Hotter arc than with argon is produced with helium if necessary. Of the two filler metals for aluminum bronze in Table II the first is preferred because it reduces hot shortness.
The second filler metal gives stronger and harder joints but lower in ductility. Preheat as above can be used if necessary.
SMAW can be used for aluminum bronze using covered electrodes indicated in
Table III above.
Preheating at 200 °C [400 °F] may be needed for thick sections and even at higher temperatures for heavier sections.
If the aluminum bronzes to be welded have more than 7 %Al, then other electrodes richer in Aluminum are used. These are intended for surfacing and are described in AWS A5.13.
Called ECuAl-C, ECuAl-D and ECuAl-E have aluminum contents of 12.5. 13.5 and 14.5 % respectively.
ANSI/AWS A5.13:2010
Specification for Surfacing Electrodes for Shielded Metal Arc Welding
Edition: 5th
American Welding Society / 24-Mar-2010 / 44 pages
Thick sections may require preheating up to 620 °C [1150 °F], and also stress relief annealing at the same temperature followed by fan cooling to avoid cracking.
Silicon Bronzes
Silicon bronzes, based on Cu-Si-Sn, are the most weldable alloys by the three processes mentioned here.
GTAW is readily done with filler metal ERCuSi-A in all positions.
DCEN (electrode negative) is applied, but zirconiated (EWZr) or pure tungsten (EWP) electrodes are preferred.
Silicon bronzes have a narrow hot short range just below the solidus and therefore, to avoid cracking, must be cooled rapidly from Welding-copper temperature through this interval.
Because of this, preheating should not be applied, inasmuch as its thermal conductivity is fairly low, lower than that of carbon steels.
The same indications are kept in mind for GMAW that is used for thickness of more than 6 mm (0.25").
Filler metal is ERCuSi-A for all silicon bronzes.
To avoid heat buildup, rapid travel speed should be adopted with no preheat, and interpass temperature should not exceed 95 °C [200 °F] to prevent hot short cracking.
SMAW, if necessary, is done with aluminum bronze electrode ECuAl-A2 but the properties obtained are substantially lower than those obtained with the other processes.
Anyhow peening may be applied to reduce residual stresses, distortion and cracks.
Copper Nickel Alloys
Copper nickel alloys are among the most resistant to aqueous corrosion, readily weldable by the three processes considered here.
GTAW is preferred for thin sections, argon is used and DCEN (electrode negative) with thoriated tungsten electrode (EWTh), preheat not required.
Filler metal ERCuNi includes 0.2-0.5 %Ti to scavenge oxygen and avoid porosity or embrittlement, and should be used also for thin sections, because base metal do not include deoxidizers.
Therefore autogenous welding (without filer metal) of thin sections should be tested to verify acceptability, as it may be found excessively porous.
GMAW is preferred for sections thicker than 1.6 mm (0.06") with ERCuNi filler metal, DCEP (electrode positive). No preheating or post heating required.
SMAW uses ECuNi covered electrode with DCEP, preferably in flat position. Slag is adherent, requiring special attention for complete removal.
Copper and alloys can be welded to dissimilar copper base or other materials, like nickel base or steels and stainless steels.
Many of the standard filler metals can be used. GTAW is used for relatively thin joints, with the arc directed to the more conductive metal being welded. Preheat may be needed.
GMAW application requires attention to the composition of the filler metal which should be compatible with both the dissimilar materials to be joined, and to the preheat temperature.
ERCuAl-A2 is considered the universal electrode, suitable for joining coppers to steels, stainless steels, aluminum bronzes, silicon bronzes and copper-nickel alloys.
This filler metal however cannot be used for phosphor bronzes. These are welded with ERCuSn-A.
In particular alloys having tendency to hot shortness or oxide formation should be examined with special attention.
In particular one should pay attention to a research that was reported in Issue 79 of Practical Welding Letter for March 2010.
Click on PWL#079 to see it.
There, in section 4, an article from the Welding Journal was quoted, reporting on a research conducted to find the reason for cracks in the welds of a long stainless pipeline.
"The investigators concluded that the cracks were due to Copper Contamination Cracking, a known cause of failure due to penetration of molten copper into the grain boundaries."
Copper contamination is indeed reported as a serious problem, but it seems connected to instances where copper was liquated from alloys or was overheated while in contact with steel (i.e. from fixtures).
Anyhow it seems reasonable to operate with caution, when welding stainless to copper alloys, and to look for possible instances "where localized Cu liquation causes grain boundary penetration and cracking".
Other Processes
Besides arc Welding-copper, other processes may be preferable in certain instances. For welding and splicing copper wires for electric appliances and electronic instruments, cold ultrasonic welding, besides soldering, may prove advantageous.
Friction Welding for suitable joints should be explored, even for dissimilar materials.
Friction Stir Welding is successfully used for more and more applications. See Canister sealing for nuclear waste - EB or FSW (Video) from TWI.
(Sorry! The direct link was removed by the source.)
[As reported in PWL#102, Sect. 5.5].
Resistance Welding is not suitable, at least for the highest electrical conductivity copper materials, because of too low resistance and insufficient heat.
High Energy Processes like Electron Beam and Laser Beam Welding may be suitable for Welding-copper in special cases to be explored.
In certain cases, other non welding processes like Brazing Copper, may be more suitable and even preferable (i.e. for joining small tubing).
* * *
Any questions or comments or feedback? Write them down and send them to us by e-mail.
Click on the Contact Us button in the NavBar at top left of every page.
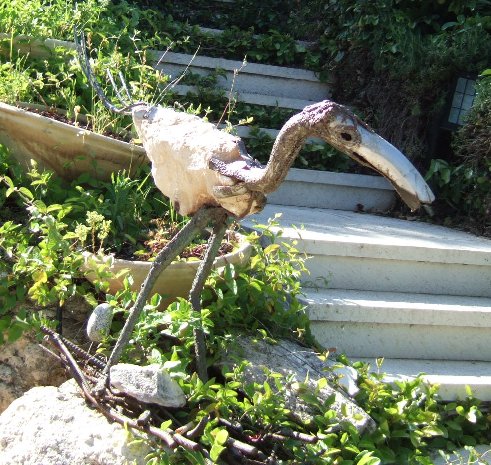
Bird by Uri Sharon
[From https://www.welding-advisers.com/Hobby-welding.html]
Let us remind you that, if you are interested, we offer a no cost subscription to our Practical Welding Letter and a bonus book in pdf format to be made available for download to your computer on the subject of
PRACTICAL HARDNESS TESTING MADE SIMPLE.
Please Subscribe.
To reach a Guide to the collection of the most important Articles from Past Issues of Practical Welding Letter, click on Welding Topics.
Note: To view Google Ads, Please
Right Click and Open in a New Window.
|
Home
Site Map
Index Page
Cast Iron Welding
Steel Welding
Alloy Steel Welding
Welding High Yield Steels
Tool Steel Welding
Stainless Steel Welding
Welding Duplex Stainless Steel
Materials
Material Identification
FAQ
Aluminum Welding
Joining Aluminum MMC
Welding Aluminum, Reprint from HIWT
Magnesium Welding
Titanium Welding
Welding Nitinol
If you did not yet find what you need, why not typing your question in the following Search Box?
Welding-copper Top
Watch the video...
Click on the following image to watch the SBI! TV Show!
POWERED BY:
Click on this Logo NOW!
Watch - The Video:
Why Don't I Work From Home?
and also
Think outside the Cube.
Follow this Invitation!
Experience C2 power and flexibility in action by clicking SBI! 2.0 For You. Where SBIers share their business-building experiences first-hand. You will realize that there is nothing comparable to SBI! when you read real stories from SBIers who share how C2 has helped them expand, accelerate, build trust and monetize their sites.
|
Copyright (c) 2003-2012, 2013, 2014, 2015, 2016, 2017
by Elia E. Levi and www.welding-advisers.com
All Rights Reserved.
Welding-copper may be difficult. Best use of high power density processes. Know the causes for porosity. Implement provisions against poisoning. See here...