Welding-cost
estimate, the power of knowledge.
Solutions with Effective Practical Advice
Estimate Welding-cost for Successful Business |
Welding Problem? Solve it! with
Help from a Welding Professional Contact Us.
|
Note: To view Google Ads, Pls.
Right Click and Open in a New Window.
|
Why Estimating Welding Costs?
Welding-cost estimate is one of the most important tools.
It helps in the economic conduction of a welding enterprise.
Unfortunately it is usually an ill understood and poorly applied practice.
Understanding the factors affecting welding costs may stimulate to apply serious changes.
Visit the NEW Page on Weld-design-review, for
avoiding costly oversight.
Visit the NEW Page on Welding Applications, for
selecting correctly the ways and means needed for productive performance.
Visit the NEW Page on Welding Problems,
for looking into the causes of production hindrances.
Welders may be afraid that such an insight might have a negative impact on their bring-home pay.
But also Managers may be reluctant to investigate in depth what is going on.
They may fear of being put in front of responsibilities they are not willing to face.
If this is indeed the case with Welding-cost estimates, it is in fact a pity.
The only logic way to make informed choices among alternatives is to know or at least to estimate the total cost of every different method.
Selection of a certain process, however, may be constrained by circumstances.
These could be available equipment, or trained workforce, or time consideration, or scarce supplies.
What has to be noted is that any choice has its Welding-cost.
It is almost incredible that in this epoch of global competition and of almost daily survival struggle with the color of the bottom line one should disregard Welding-cost estimate as an annoying nuisance.
Note: To view Google Ads, Please
Right Click and Open in a New Window.
|
Know your Welding-cost
It appears that the Truth may be disturbing if one lacks the courage to face it and to do something about.
As a simple exercise, next time you stroll in the welding shop, just ask the person in charge what is the filler metal weight used per unit weld length, or per hour, of the three most important welding jobs currently being performed.
This is called the Weld Deposition Rate.
Ask also: how do you know?
Any answer that is not based on calculations should be rejected. This exercise will give you a measure of the ignorance.
Also a small job shop may have difficulty in realistically evaluating its own Welding-cost estimate.
But it must be stressed that a correct evaluation may sometimes mean the difference between success and bankruptcy.
A simplified version of Welding-cost estimate as applied to the case of Hardfacing has been dealt with briefly in issue #05 of Practical Welding Letter for January 2004.
You can see it by clicking on PWL#005.
In this page we are going to expand on the same Welding-cost estimate subject, to cover different processes and practices. In general it should be noted that good welding is that which provides the required properties at the least possible cost.
Once the designed quality is assured, there is no point in over welding, a poor practice that should be always discouraged because it may throw costs out of control.
A responsible attitude to the conduction of a successful welding activity presupposes full documentation on applicable procedures and means of control of their continuing application.
It all starts, obviously, with correct design (see Welding Design) that should strive to minimize the amount of filler metal required and make sure that joints are readily accessible to welding operations.
Standardization of types, shapes and sizes may play a role in reducing welding costs.
When evaluating the single items as indicated below, one should make sure to be consistent in the reference term. Here we propose to refer either to the total project, or to the single voices calculated "per hour". When you select a reference, stick to it.
For a thorough treatise on Economics of Welding and Cutting readers are urged to look for Chapter 12 beginning at page 483, of the same title in the AWS Welding Handbook, Ninth Edition, Volume 1.
It is a chapter full of information, with complete explanation and clear breakdown of the various terms to be included in a realistic Welding-cost estimate.
AWS WHB-1.9
Welding Science and Technology
Welding Handbook, 9th Ed., Vol. 1
American Welding Society, 01-Jan-2001
Welding-cost estimate
Welding-cost estimate is calculated by summing up all the terms bringing a contribution to the total cost of any particular job, referred to the same unit, be it length of weld or unit time, mostly hour.
Total Welding-cost for any given job is therefore the sum of the following terms:
- Base metal cost
- Preparation cost
- Weld Labor cost
- Filler Metal cost
- Gases cost
- Equipment cost
- Energy cost
- Overhead cost
- Inspecting cost and
- Finishing cost
1 - Base metal cost.
This is the cost incurred for procuring (including custom dues), transporting, insuring, handling, storing, testing and bringing all the material in the proper sequence, quality and quantity at the place of erection, ready to be prepared for welding.
These Welding-cost details are best evaluated for the whole structure, be it a ship or a bridge, or for substantial sub-assemblies, clearly identified.
From these costs one can deduct the income obtained from reselling any surplus or scrap or unused reserve.
2 - Preparation cost.
The cost of cutting to dimension each single piece of metal, of beveling as required, of fixturing, of tack welding (if performed by a workforce different from the welders), of positioning, of preheating if required and of all other needed non welding activity, can sum up to substantial outlays. Elevated Welding-cost expenses are incurred when tying up major lifting equipment for long stretches of time.
As the flat position is the easiest and most practical for obtaining quality welds, it makes sense to try to perform most of welding in flat position: this may require the use of positioners, whose justification is again a question of Welding-cost estimate.
The cost of procuring, maintaining and operating specific lifting and positioning equipment required for the job, must be properly accounted for and summed to the total.
As a consequence of the above facts it is documented that important shipyards invested considerable amounts of time and of financial outlays in order to optimize procedures in Hybrid Laser-Arc (GMAW) equipment, with the purpose to be able to complete welding of thick plates from one side only.
A note on Laser Hybrid Welding was published in Issue 16 of Practical Welding Letter for November 2004. Click on PWL#016 to read it. See also: Hybrid Welding
Interested readers can download the sample Chapter on Hybrid Laser Arc Welding from ASM International Handbook, Volume 6A, from the instructions published at 14.1 in issue PWL#100. Whoever is interested can still do just that, as long as ASM keeps the promotion valid.
Pre-weld cleaning operations may be critical, depending on materials, for the success of welding: they have to be planned, implemented, completed, inspected, and accounted for.
Set up preparation, alignment and measuring of gaps and distances are recurring operations: the implementation of wisely conceived fixtures and measuring aids may influence favorably the outcome by reducing the time needed in preliminary non-welding activities.
3 - Labor Welding-cost.
This is one of the most expensive elements contributing to the total weld cost. It should be accounted for properly because careful attention could suggest ways and means to increase productivity by any change that permits a reduction of the total workforce for the job.
Among the provisions, the use of more suited positioners or fixtures, and employing helpers, whose pay rate is generally lower than that of welders, may increase significantly the welder's time devoted to welding, removing accessory activities not connected to welding proper.
Weld labor is usually accounted for as an hourly rate, which will be different for different welders depending on their experience, skill, ability, versatility etc. Accessory insurance and social security expenses may or may not be included: if not these should sum up with Overhead. It makes sense to sum up all the labor expenses for welding a given unit of the job, to assess its labor cost, but for comparison of different processes the expense should be referred per hour.
Operator or operating factor describes the percentage of time that a welder employs in actual welding (arc-on time or flame-on time), with reference to the total time that the welder is physically present in the workplace.
Efforts should be implemented to improve Operating factor. Therefore welding operations should be planned and positioned to minimize welder's physical fatigue and to ensure safety and maximum comfort.
This maybe a delicate concept, because the commitment to improve this factor may be interpreted as a will to exploit the welder's energy to the maximum with the consequence of impairing his/her well being.
This same concept however can be used as an incentive, to grant bonus or advancement to those welders consistently engaged in providing an operating factor above the average. And for those suggesting aids or means to improve it. For effective use an impartial and practical way of recording actual arc-on time should be conceived and implemented.
Operating factor values commonly accepted in the welding industry range from 30 to 50%. This is one of the reasons most commonly reported for management push to switch, if possible, to automatic or robotic welding, where in principle the operating factor should be much higher than for manual operation, and constant in time (except for breakdowns).
Good practice suggests striving for obtaining good quality at the first attempt, in order to minimize unnecessary operations like repair, rework and reinspect, which increase the costs without providing any gain or advantage in the business.
Whenever rework exceeds a predetermined low maximum limit, it is time to investigate the causes and to look for adequate remedies to improve the performance of the whole operation.
An article on Five Goals for Improving Productivity was published (2) in Issue 80 of Practical Welding Letter for April 2010.
Click on PWL#080 to read it.
4 - Filler metal cost.
Handbooks report tables for calculating the required volume of filler metal theoretically needed to fill any given joint shape and size. While these data may help to provide Welding-cost estimate in advance, a simple record keeping performed while actually welding may be adequate for obtaining real data. And it is the current updating of this information that will advise if something is running out of control.
Working with the correct size of filler metal has a direct influence upon the Welding-cost. A smaller size of electrode permits to increase current density, which may have influence upon penetration. A larger size permits working with higher current, with consequent higher volume of metal deposited per unit time. In Shielded Metal Arc Welding, the average length of discarded stubs is also a factor to consider.
The selection of the size to be adopted therefore should not be left to chance or to welder's feeling, but should be objectively documented as that producing the least Welding-cost per unit of comparison adopted (length or weight of deposited filler metal per working hour).
Deposition efficiency is defined as the ratio, expressed in percentage, of the theoretical weight (volume multiplied by density) of the joint material needed per unit length, to the actual weight of filler metal consumed per unit length. This can be best calculated from raw data or assumed if based on previous experience.
If we calculate from the geometry of the joint section or if we obtain it from handbook's tables the theoretical weight of filler needed per unit length of joint, we can get the actual weight of filler required per unit length, by dividing the first by the deposition efficiency (smaller than 100%).
If we know the weight of filler metal necessary to weld one unit of length (meter or foot) of that given joint and if we know the number of unit lengths welded in one hour, by multiplying the two we get the weight of filler metal used per hour. This is called the Weld Deposition Rate, a most important datum useful for comparing processes and for assessing the influence of any other variables intervening in the welding of the same joint.
By multiplying this result by the cost of filler metal per unit weight we get the Welding-cost of filler metal consumed in an hour.
5 - Gases cost
This cost intervenes only when auxiliary gases are actually used in the process. In this case the cost of gas per hour (including welding and non welding time when flow is zero) is obtained by the hourly consumption rate (gas volume flow used) multiplied by the Operating factor or efficiency (the welding time to total time ratio), multiplied by the cost of the gas expressed per hour of flow.
6 - Equipment Welding-cost.
The equipment selected should be adequate in power so that the requirements of its duty cycle (percentage of working time admitted in any ten minutes period, to allow for cooling down) will never reduce the operating factor achievable.
The easiest way to account for equipment is to record the rental cost, if the equipment is indeed rented. Otherwise the Accounting department should come up with a cost per hour or per day for each of the main pieces of equipment, including purchasing cost, cost of capital, depreciation, maintenance costs and spare parts costs.
In certain cases, for expensive equipment like a robotic cell, or an Electron Beam Welder, or an automatic resistance welding machine, this cost may be the highest expense of the facility, hopefully covered by the high productivity of the unit, reducing to the minimum the cost per weld.
7 - Energy cost.
For electric equipment the Welding-cost estimate should be calculated by multiplying Voltage by Amperage and dividing by 1000 and by the electric efficiency of the equipment, times the price per kWhr (kilo Watt hour) time the operating factor (actual arc-on time per hour).
In case of a gasoline engine driven power generator, the hourly energy cost would be that of the gasoline used up in an hour of normal work.
When using electrically heated furnaces or other implements for preheating or post heating, the cost of energy used for heating should be estimated and accounted for.
8 - Overhead cost.
Overhead costs include all expenditures that it is not practical to account for individually but that when summed up amount to a considerable outlay. They include office costs, all indirect personnel costs, taxes, insurance, transportation, advertising and sales, and also auxiliary consumables not specifically devoted to any identified job.
To protect from underestimating, overhead should be conservatively estimated on the high side when in doubt, to compensate for overlooked expenses.
In practice it will usually be defined as a certain percentage of Labor costs (i. e. 150%) but any rate may be valid although some effort should be exerted to attempt a realistic figure.
9 - Inspection cost
For demanding application inspection costs may involve the employment of sophisticated techniques (Ultrasonic Testing and/or Radiographic Inspection) and of expert technicians to carry them out. But even in the simplest of cases, at least Visual Inspection must be performed thoroughly and in a professional way.
As indicated in an article published in the April 2004 issue of Practical Welding Letter No. 08, (Click on PWL#008 for reading) there may be the temptation to charge the welders with this inspection.
While it is good practice that welders inspect their own work for themselves, it is questionable if the decision to economize on dedicated Visual Inspectors is a wise one. For one thing, this decision decreases the Operating factor, by reducing time devoted to welding: at least one should account for the cost of this decision and be ready to justify it.
Inspection costs depend mainly on quality requirements and will be generally accounted for whole projects. The cost "per hour" is probably not quite meaningful. Therefore summing up can correctly be performed only if all terms are equally calculated for whole projects.
10 - Finishing cost
A certain number of operations may be required after all welding is completed. Again these costs are best calculated for whole projects.
There may be final cleaning and grinding, spatter removal, post weld heat treatment cycles, painting, assembling for erection or disassembling for transportation and any other activity specified in the purchase order.
These operations may need auxiliary products and application means that must be provided, operated and accounted for.
A brief note containing links to Resources for preparing a Business Plan was published in the issue No. 18 of Practical Welding Letter of Feb. 2005. To see the contribution click on PWL#018.
See also our new page on Welding Management.
An Article on Managing Welding Costs was published (7) in issue 98 of Practical Welding Letter for October 2011.
Click on PWL#098 to see it.
For a scientific based process of cost reduction through removal of Waste, see the Article on Process Optimization and Innovation, published (2) in Issue 102 of Practical Welding Letter for February 2012.
Click on PWL#102 to see it.
An Article on Early Inspection for Higher Productivity was published (2) in Issue 110 of Practical Welding Letter for October 2012.
Click on PWL#110 to see it.
An Article on Learning from Experience was published (2) in Issue 135 of Practical Welding Letter for November 2014.
Click on PWL#135 to see it.
To receive at no cost every issue of this publication, please subscribe.
Conclusion
There is no mystery in Welding-cost estimate: it is mainly a question of common sense. But it must be appreciated that correct accounting for total Welding-cost incurred in a welding operation is a preliminary requirement to the assessment of the best practices and a necessary tool for the economic management of any welding enterprise.
If you did not yet find what you need, why not typing your question in the following Search Box?
Watch the following Video on
How to Calculate Cost per Kg of Welding Metal https://www.youtube.com/watch?v=J-hdIb4Q-AY |
* * *
Any questions or comments or feedback? Write them down and send them to us by e-mail.
Click on the Contact Us button in the NavBar at top left of every page.
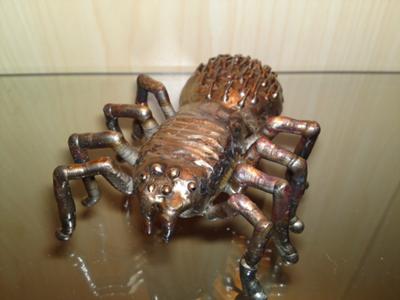
Untitled
[From https://www.welding-advisers.com/100-stainless-steel.html]
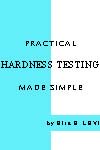
Have you already subscribed to your FREE copy of Practical Welding Letter and downloaded your FREE copy of our booklet in pdf format on PRACTICAL HARDNESS TESTING MADE SIMPLE? If not yet just Subscribe.
You might find a few items interesting to you, related to your welding activity.
To reach a Guide to the collection of the most important Articles from Past Issues of Practical Welding Letter,
click on Welding Topics.
Note: To view Google Ads, Please
Right Click and Open in a New Window.
|
Back Home
Site Map
Welding Economics
Starting a Welding Shop
Welding Management
Managing Welding
Welding Positioner
Monitoring Structures
Production Failures
Outsource Welding
Welding Planning
SAFETY
Fume Hazards
Fire Prevention
Hobby and Home Welding
Welding Projects
Welding Control
Welding Testing
Welding Qualification
Welding Inspection
Welding-cost Top
Watch the following Video...
POWERED BY:
Click on this Logo NOW!
Watch - The Video:
Why Don't I Work From Home?
and also
Think outside the Cube.
Follow this Invitation!
Experience C2 power and flexibility in action by clicking SBI! 2.0 For You. Where SBIers share their business-building experiences first-hand. You will realize that there is nothing comparable to SBI! when you read real stories from SBIers who share how C2 has helped them expand, accelerate, build trust and monetize their sites.
|
Copyright © 2004-2010, 2011, 2012, 2013, 2014, 2015, 2016, 2017
by Elia E. Levi and www.welding-advisers.com
All Rights Reserved.
Welding-cost estimate is a must do task, just to know where one stands and what to do to improve. See it all here...