Welding-defects
to avoid and correct:
SOLUTIONS with Effective, Powerful Advice
Always Prevent Welding Defects
|
Welding Problem? Solve it! with
Help from a Welding Professional Contact Us.
|
Note: To view Google Ads, Pls.
Right Click and Open in a New Window.
|
Are any minor flaws Welding-defects? No.
(See further down).
Welding defects must be prevented but, when found, must be removed and corrected.
In a previous page on WELDING FAILURES, we expressed the opinion that failures occur only in service.
We imply by this that Welding-defects should not be allowed out of the production line.
But human activities being what they are, it is probably unrealistic to exclude at all the chance that from time to time defective structures be put into service.
Visit the NEW Page on Welding Overview, for a thorough Introduction to Welding.
Visit also the NEW Page on Process-selection, for Understanding the Selection procedure and
the NEW Page on Process-optimization for improved productivity.
It is however under the responsibility of the person in charge of a welding operation to strive to reduce to the minimum such occurrences.
What are Welding-defects?
Welding-defects are excessive conditions, outside the acceptance limits of deviations, which risks to compromise the stability or the functionality of the welded structure.
They are also called rejectable discontinuities. This means that the same type of discontinuity of a lesser degree, might be considered harmless and acceptable.
Are there acceptable Welding-defects? No, by definition a defect is rejectable. There can be acceptable discontinuities.
The designer, the purchaser, or the person in charge of the welding project are entitled to define the limits of acceptance. These limits are valid only for the application and the usage involved.
Are there undetected defects? Hopefully not! No Welding-defects should go undetected. Undetected discontinuities should be only those acceptable, as defined by the designer.
What should be done when Welding-defects (unacceptable discontinuities) are detected? One should reject the items and put them temporarily on hold.
One should determine the cause of that happening and try to implement a corrective action to avoid future recurrence.
Then an authorized professional should determine if the defects are repairable or not. If yes by which procedure. Standard procedures may be approved for routine application.
If not, the rejected item, however expensive in materials and working hours invested, should be tagged with a red Reject Tag and thrown into the junk bin.
An Article on Failures from weld Discontinuities is included in our Practical Welding Letter No. 11 of July 2004.
To read the article click on PWL#011.
An Article including considerations on Weld Defects and on the importance of investigating the reasons of their appearance, for eliminating their recurrence, was published in Issue 28 of Practical Welding Letter for December 2005.
To read the article (in Section 2) click on PWL#028.
An article of ours, was published on July 11, 2006 in the magazine The Fabricator.
It can be found by clicking on Arc Welding Discontinuities.
An Article on Lamellar Tearing was published (7) in Issue 46 of Practical Welding Letter for June 2007.
Click on PWL#046 to read it.
Issue 131 of Practical Welding Letter for July 2014 includes Section 6
Terms and Definitions Reminder dedicated to Welding Defects.
It can be found by clicking on PWL#131.
An Article on How to Prevent Defects in arc welded Aluminum was published (7) in Issue 166 of Practical Welding Letter for June 2017.
Click on PWL#166.
To receive all the issues of PWL as they are published, please Subscribe.
If you did not yet find what you need, why not typing your question in the following Search Box?
Note: To view Google Ads, Please
Right Click and Open in a New Window.
|
Definitions...
What is the difference between discontinuities and defects?
A discontinuity is an objective lack of material, an interruption in the physical consistence of a part.
Examples are cracks, seams, laps, porosity or inclusions. They may or may not be considered defects depending if their presence endangers or not the integrity, the usefulness and the serviceability of the structure.
By knowing what is likely to produce Welding-defects one should learn how to prevent them. It is essential to distinguish discontinuities from harmful defects.
Production without defects saves work-time, materials, repair costs, decrease in productivity. Excessive defect production indicates some basic condition affecting the operation which should be investigated and corrected.
Causes for rejection and how to avoid Welding-defects.
Avoidance of Welding-defects starts with correct design and preparation. This may look as an obvious statement but somehow it is a situation more frequent than desired.
There is no point in trying to correct by welding for misalignment or for improper set up of the workpiece.
There is no gain in time, really, only an increased probability of producing Welding-defects and of spending time and resources in trying to repair the welded item.
Also the use of recommended tools and fixtures should be implemented with no excuses admitted for temporary unavailability.
The required means, in good operational condition, should be used with the correct parameters, according to the approved procedure.
If the present welding procedure is incapable of ensuring defect free implementation, then it should be improved upon before resuming operation.
The welder or the machine operator should be proficient in the process selected and all physical accessories assigned should be ready for use. Among them, all safety accessories like aspirators of fumes, fans to circulate air, screens to protect other workers nearby, etc.
If electrodes need be dried, so they should be. Cleaning of fixtures and workpiece should be performed before setting up. A last touch up may be repeated just before welding.
Types of Welding-defects.
DIMENSIONAL Welding-defects can be assessed by visual inspection and by measuring with simple weld gauges. They derive from improper set up or by distortion which should be controlled in a proper fixture, or by a different welding sequence.
In general they should be corrected by employing proper means before welding. MISALIGNMENT is a setup problem.
Other appearance features which may cause rejection of these Welding-defects are excessive bead convexity and reinforcement, or the opposite condition, namely considerable concavity and undersized welds. Here the welder's technique should be improved.
UNDERCUT consists in a groove formed into the base metal, adjacent to the weld bead. It derives from improper manipulation of torch or electrode. Further training and improved skill of the welder should save future performance.
CRACKS are never permitted, because they are seen as stress raisers, and capable to grow until fracture.
Different forms and positions of cracks can hint at their origin, and should be investigated before trying to correct for their appearance.
Except for cases of lack of experience of the welder, who may be unable to end a weld bead without crater cracking, other instances derive mostly from limited weldability of the materials.
That should be dealt with by whoever has metallurgical experience, by means of special procedures invoking pre-heat and post heat and other tricks which the welder cannot be expected to provide.
Welders should be expected only to perform exactly their job as prescribed in the relevant Welding Procedure Specification.
Fine cracks that cannot be seen by visual inspections, are the object of specialized inspection techniques. See NON DESTRUCTIVE TESTING in WELDING INSPECTION.
More Welding-defects...
POROSITY is a condition caused by gases remaining entrapped in the melt.
This pertains generally to internal Welding-defects, which can be detected either by sectioning (which is a destructive test) or by special non destructive testing like radiography or ultrasonic testing.
If this condition is determined, one should eliminate the cause, be it the material, or humidity in the electrode sheathing, or gases from excessive heat and turbulence in the melt or incorrect manipulation (improve skill).
A new page on Weld Porosity can be reached by clicking on this underlined link.
Among other important Welding-defects one should strive to eliminate the following.
INCOMPLETE FUSION, which is generally assessed by sectioning the joint (mostly a test piece) and finding the unmelted base metal that outlines the original joint shape.
And INADEQUATE PENETRATION that means that the weld bead extends from its face only to a limited distance, less than what is required by the procedure.
NON METALLIC INCLUSIONS (in Shielded Metal Arc Welding) usually refer to Welding defects in the form of slag being trapped in the melt, generally meaning insufficient skill of the welder.
It could also mean oxide inclusion, in all types of welding, or tungsten metal, in Gas Tungsten Arc Welding. All these conditions can be detected either in a section or by non destructive inspection techniques.
RESISTANCE WELDING has its own set of unacceptable defects per Specification, to be determined at the stage of schedule approval by destructive testing.
Shear Strength, a common Specification requirement, is determined by mechanical testing of spot welded coupons.
The shape and dimensions of the weld nugget, and the appearance of Welding-defects in the form of internal cracks or inadequate fusion are determined by destructive examinations under a microscope of a section of cut up specimens, ground, polished and etched.
At the production stage one should put the utmost care in manufacturing acceptable joints because it is the least expensive solution. Most of the Welding-defects are visible. The welder should be encouraged to inspect his/her own weld. Inexperienced welders should be asked to seek advice from more skilled fellow workers, and to look for help for repair in order to avoid just a cover up.
Failures in service can come up for reasons different from manual welder's skill. But this is another subject that is being dealt with in a page on SERVICE FAILURES
NEW RESOURCES
Find some interesting links in a special Mid Month Bulletin Page of our PRACTICAL WELDING LETTER, designed offer you, our interested readers, the opportunity to search the web quickly and effectively on the subject of Welding Failures and related Subjects.
We urge you to explore this rich source of essential knowledge. Online Resources on Failure Analysis, Root Cause Determination, Physical Survey, Evidence Collection, Witness Information, Metallurgical Investigation, presenting Articles, Downloads, Links and Information is now available by clicking on PWL#053B. |
See also the Special Mid Month Bulletin 20 listing Online Resources on Welding Defects, Welding Discontinuities, Types of Defects, Visual and Dimensional Defects, Internal Defects, Finding and Repairing Defects and more...
Click on Bulletin 20.
Looking for more Online Reference Links? Click on Welding Resources
Watch the following Video on
Welding Defects
https://www.youtube.com/watch?v=P6NXS4N5iuU |
* * *
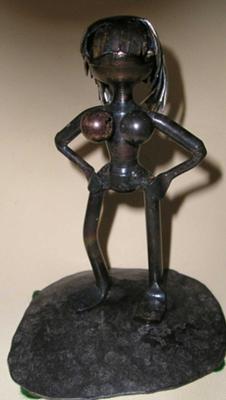
Oly54
[From https://www.welding-advisers.com/oly54.html]
Any questions or comments or feedback? Write them down and send them to us by e-mail.
Click on the Contact Us button in the NavBar at top left of every page.
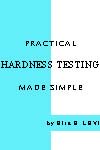
Have you already subscribed to your FREE copy of Practical Welding Letter and downloaded your FREE copy of our booklet in pdf format on PRACTICAL HARDNESS TESTING MADE SIMPLE?
If not yet, just click here for your PWL Subscription.
You might find a few items interesting to you, related to your welding activity.
To reach a Guide to the collection of the most important Articles from Past Issues of Practical Welding Letter,
click on Welding Topics.
Note: To view Google Ads, Please
Right Click and Open in a New Window.
|
Back HOME
Back to Site Map
Back to QUALITY
Welding Design
Welding Codes
Welding Control
Welding Testing
Welding Inspection
Weld Cracking
Welding Failures
Welding Liability
Weldability Testing
Visual Weld Inspection
Welding Validation
Starting a Welding Shop
Welding Cost Estimate
Welding Management
Welding Positioner
Welding-defects Top
Watch the following Video...
Click on the following image to watch the SBI! TV Show!
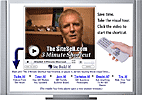
POWERED BY:
Click on this Logo NOW!
Watch - The Video:
Why Don't I Work From Home?
and also
Think outside the Cube.
Follow this Invitation!
Experience C2 power and flexibility in action by clicking SBI! 2.0 For You. Where SBIers share their business-building experiences first-hand. You will realize that there is nothing comparable to SBI! when you read real stories from SBIers who share how C2 has helped them expand, accelerate, build trust and monetize their sites.
|
Copyright (c) 2003-2008, 2009, 2010, 2011, 2012, 2013, 2014, 2015, 2016, 2017
by Elia E. Levi and www.welding-advisers.com
All Rights Reserved.
Welding-defects are the worst enemies of successful production. Considerable effort should be spent to learn to detect and avoid them. Look here...