Welding-distortion:
how to prevent and control.
SOLUTIONS with Effective, Powerful Advice
Welding Distortion Prevention: a Major Problem |
Welding Problem? Solve it! with
Help from a Welding Professional Contact Us.
|
Note: To view Google Ads, Pls.
Right Click and Open in a New Window.
|
Welding-distortion: why straight welds become crooked?
- The unavoidable nature of Welding distortion and its causes are explained here.
- How to reduce Welding distortion?
- What happens to fixtured welds?
- Are residual stresses harmful?
- How can one see the effects of residual stresses?
Visit the NEW Page on Welding Overview, for a thorough
Introduction to Welding.
Visit also the NEW Page on Process-selection, for
Understanding the Selection procedure and
the NEW Page on Process-optimization for improved productivity.
Here is a reminder about Welding distortion. Understanding these and related causes and effects will:
- improve your mastering of the processes,
- save your time by avoiding predictable distortions,
- let you find practical solutions,
- improve quality,
- reduce scrap and rework,
- increase productivity.
The effects of residual stresses
Here we are dealing in some more detail on the subject of Welding-distortion, whose control finds an important place in well built procedures.
Why Welding-distortion occurs, causing warping?
Welding-distortion or deformation or warping of weldments during welding is a natural outcome of intrinsic non uniform heating and cooling of the joint.
Welding-distortion is the result of the action of internal stresses which are produced while welding.
Residual Stresses are those remaining in the part or construction after heating is removed, as briefly explained in the following.
Stresses are due to volume changes with heating and to decreasing yield strength at elevated temperature.
Metal subject to thermal expansion while heating tends to be compressed by the surrounding cool structure.
The expanding heated volume has now lower yield strength at high temperature, and therefore it is easily upset (deformed) to shorter dimensions.
Upon cooling the same material tends to contract in all directions.
But by now the yield strength is again higher, at lower temperature, so that the upset material cannot regain its original dimensions.
The main dimension of the heated volume above, which was deformed (upset), is now shorter than it was before welding.
But, while cooling down, it cannot reach the previous dimension because the attached cool structure, which did not move appreciably in the process, will not let it.
Therefore that volume, that was first heated, shortened (upset) and then cooled, in now pulled in tension by the surrounding structure that was not heated.
The result is the development of internal tension stresses in the weld. These residual stresses are the cause of Welding-distortion.
If you did not yet find what you need, why not typing your question in the following Search Box?
Note: To view Google Ads, Please
Right Click and Open in a New Window.
|
How to decrease...?
Sometimes to decrease the amount of Welding-distortion it is sufficient anticipate the deformation occurring, and to counter it by an opposite displacement before welding.
If two plates being welded are rotating one toward the other while being welded, this amounts to place the elements at an angle before welding, in order to counter the movement by a certain opposite displacement.
Or (for butt welds) to weld a short length at one end and then start again from the other end, while the first end is already rigidly welded.
Otherwise one can distribute short stretches of welding at distant places, by introducing sequences aimed at avoiding local concentration of heat input.
Fixturing assemblies and sequencing short weld beads
Or one can provide very rigid fixturing that will not allow any movement while welding is performed. Movement can be prevented: residual stresses cannot.
One can easily prove that the part is now highly stressed (presenting a high level of residual stresses).
After taking the part out from the fixture if one removes some of the weld by partial asymmetric cutting or grinding, the remaining portion will deform considerably to rearrange the remaining internal stresses.
This Welding-distortion is an indirect proof of the high level of stresses which were present in the as welded part.
Material removal is at the base of certain methods of residual stresses measurement.
Occasionally when the residual stresses exceed material strength, cracks may appear in the weld at high temperature or while cooling near room temperature.
See AWS standard C4.4/C4.4M:2007,
Recommended Practices for Heat Shaping and Straightening with Oxyfuel Gas Heating Torches,
that provides guidance on what to do and what
not to do to avoid or correct distortions in welded structures.
Why stress relieve...?
It is good practice to relieve the residual stresses of a constrained welded assembly.
The reason is that these stresses can sum up with external stresses in service and exceed the material strength, producing failure, or further deformations.
The most common method of stress relieving for reducing Welding-distortion, is performed by heating the welded assembly in a suitable furnace.
Heating the welded structure uniformly in a furnace at elevated temperature, causes the remaining maximum stress to be reduced to the yield strength value of the material at that temperature, which is lower than it was at room temperature.
During stress relieving some minor relative movements will take place.
Upon cooling, the residual stresses will stay significantly reduced.
Another method uses mechanical peening of the weld either by hammering or by shot peening equipment: this is done sometimes on tool steels immediately after shielded metal arc welding and before cool down.
A short Article on Stress Relieving after Welding was published in the issue 8 of Practical Welding Letter, Section 7, for April 2004.
To see the article click on PWL#008.
Vibrational stress relief, uses sub-harmonic frequencies to reduce any residual stresses, by introducing mechanical energy into the work piece.
A short note on Vibrational Stress Relief was published in the issue 15 of Practical Welding Letter (Section 9.5) for November 2004.
To see the note click on PWL#015.
Relieve stresses to stabilize structures
The above is correct for a simple metal like plain low carbon steel where no metallurgical phase changes take place.
In more complex cases, phase transformation comporting volume changes can intervene, complicating the issues and the solutions.
The general approach would be to reduce the causes of Welding-distortion by providing suitable pre-heating, if possible, so that there will be less expansion difference, between material at weld temperature and surrounding structure.
The actual determination of residual stresses after any of the above methods is done by specialized technologies.
Among these are:
- a destructive method that provides precise measuring by strain gages application of tiny movements or strains subsequent to strategic cuts in the material,
- x-ray diffraction (a nondestructive method that measures the deformation of metallic crystals), and
- ultrasonic measurement of residual stresses (study of acusto-elastic properties).
A short note on Welding Distortions was published (3) in Issue 66 of Practical Welding Letters for February 2009.
Click on PWL#066 to see it.
The reference to a page on Residual Stresses was published (8) in Issue 80 of Practical Welding Letters for April 2010.
Click on PWL#080 to see it.
A practical note on Straightening a Pipe Distorted by Welding was published (11) in Issue 83 of Practical Welding Letter for July 2010.
Click on PWL#083 to see it.
An Article on Controlling Distortion was published (3) in Issue 104 of Practical Welding Letter for April 2012.
Click on PWL#104 to see it.
An Article on Filler Metal for Controlling Welding Distortion was published (4) in Issue 132 of Practical Welding Letter for August 2014.
Click on PWL#132 to see it.
An Article on Distortion Control was published (3) in Issue 162 of Practical Welding Letter for February 2017.
Click on PWL#162.
An Article on Using flame to redress distortions in Stainless Steels was published (3) in Issue 164 of Practical Welding Letter for April 2017.
Click on PWL#164.
The following website pages may help in clarifying some of the concepts involved in the subject of this page. Click on the links.
Residual Stress.
Stress Relieving.
Weld Preheating.
NEW RESOURCES
Find some interesting links in a special Mid Month Bulletin Page of our PRACTICAL WELDING LETTER, designed offer you, our interested readers, the opportunity to search the web quickly and effectively on the subject of Welding-distortion and Prevention We urge you to explore this rich source of essential knowledge. Online Resources on Welding Distortion and Prevention, presenting Articles, Data, Properties, Downloads, Links and Information is now available by clicking on PWL#048B.
Click also on PWL#104B for new Resources on Welding Distortion Prevention.
|
Looking for more Online Reference Links? Click on Welding Resources
* * *
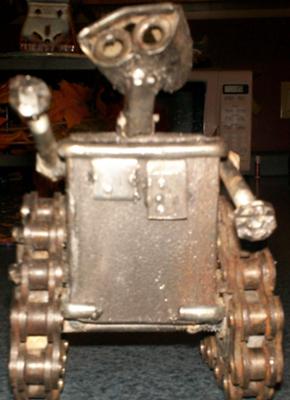
WALL-E
[From https://www.welding-advisers.com/the-wolfwolf-studio.html]
Any questions or comments or feedback? Write them down and send them to us by e-mail.
Click on the Contact Us button in the NavBar at top left of every page.
Let us remind you that, if you are interested, we offer a Free subscription to our Practical Welding Letter and a Free book in pdf format to download to your computer on PRACTICAL HARDNESS TESTING MADE SIMPLE. Click to Subscribe.
It might help when welding unknown materials.
To reach a Guide to the collection of the most important Articles from Past Issues of Practical Welding Letter,
click on Welding Topics.
Note: To view Google Ads, Please
Right Click and Open in a New Window.
|
Back Home
Site Map
JOBS
Material-identification
Welding Education and Training
Welding Design
Welding Codes
Welding Information
Welding Procedures
Welding Properties
Welding Failures
Weld Cracking
Welding Liability
Weldability Testing
Visual Weld Inspection
Welding Validation
Monitoring Structures
Service Failures
Welding Metallurgy
Residual Stress
Welding-distortion Top
Watch the video...
POWERED BY:
Click on this Logo NOW!
Watch - The Video:
Why Don't I Work From Home?
and also
Think outside the Cube.
Follow this Invitation!
Experience C2 power and flexibility in action by clicking SBI! 2.0 For You. Where SBIers share their business-building experiences first-hand. You will realize that there is nothing comparable to SBI! when you read real stories from SBIers who share how C2 has helped them expand, accelerate, build trust and monetize their sites.
|
Copyright (c) 2003-2008, 2009, 2010, 2011, 2012, 2013, 2014, 2015, 2016, 2017
by Elia E. Levi and www.welding-advisers.com
All Rights Reserved

Welding-distortion, natural and inevitable consequence of internal stresses built in a structure while welding. What can be done to limit their extent...